The link between rotating machine reliability and the hydrodynamic bearing
July 03, 2020

Proper component care pays dividends for equipment functionality
Author’s Corner: Lionel Pellevoisin is a French expert in hydrodynamic bearing technology. Since the 2000s, he has managed SAMR SAS, which manufactures and sells plain bearing bushing worldwide.
The reliability of rotating machines
Since the invention of the wheel, and even, according to some experts, the potter’s wheel that preceded it, the reliability of the machines has been a prime concern for operators.
The reliability of rotating machines is a major challenge for the industry. A process machine provides the expected production and therefore generates invoicing and customer satisfaction.
These positive results come from the adequacy of the machine, correct installation, proper operation, monitoring and maintenance. The majority of those factors put plenty of pressure on the maintenance managers of industrial sites.
One of the major components that provide proper functionality is the sliding bearing. The component’s origins date back a few millennia before the Christian era when the potter’s wheel and wheel became popular. It was necessary to control the friction and wear of an axle in its housing. The choice of materials, their sizing, the addition of a lubricant, are all problems that have appeared and accompanied the development of mechanics.
At first glance, we noticed the three technologies – the sliding bearing, the rolling bearing and, more recently, the magnetic levitation. We won’t worry about the last two, which have their limits for functional, technical or economic reasons. Instead, we’ll focus on the sliding bearing, which is a constant and essential component in high-power industrial machines.
Although it is the ancestor of bearings, the sliding bearing is the most advanced mechanical component since the industrial revolution, thanks to the materials used and the calculation capabilities made possible by computer technology. More precisely, this family is divided into two branches. The first is the friction bearing where only the friction coefficient controls the efficiency. The second is the hydrodynamic bearing. It is here that we enter an extraordinary, unknown and mysterious world.
Read the rest of the story here.
This article was originally published in the March 2020 issue of COMPRESSORTECH2. We only publish a fraction of our magazine content online, so for more great content, get every issue in your inbox/mailbox and access to our digital archives with a free subscription. Click here for a new subscription or here to renew your current subscription.
MAGAZINE
NEWSLETTER

CONNECT WITH THE TEAM
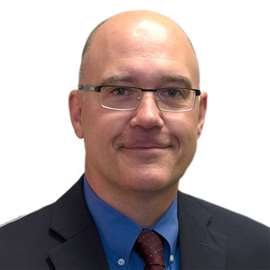
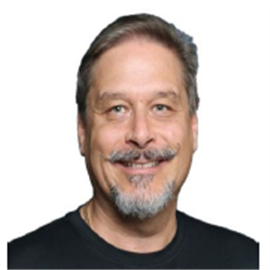
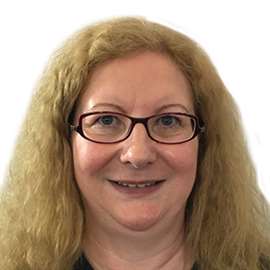
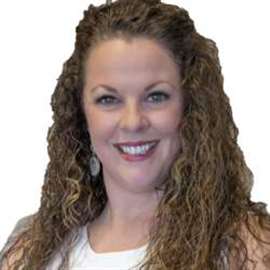