The Ingersoll-Rand rotary gas engine
March 05, 2024
The Cornerstones of Compression series has highlighted many significant products over more than 160 years of continuous progress. However, there were also some great engine and compressor ideas that were unsuccessful. This brief Cornerstones of Compression corollary series features several development failures.
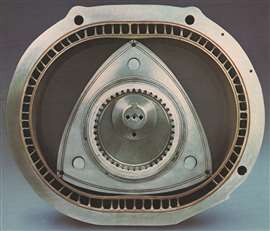
The rotary engine concept originated with Felix Wankel in Germany in 1929, but it wasn’t commercially successful until shortly after World War II. In the U.S., Curtiss-Wright led early advancement of the Wankel concept for airplane engines, and through licensing, also for automobile engines. In the Wankel engine, the four strokes of an Otto cycle occur in the space between each bow-shaped face of a symmetric triangular rotor and the inside of an oval-like epitrochoid housing. The rotor is mounted eccentrically on the output shaft with gearing, such that the rotor turns at a slower speed than the output shaft. The simple, compact rotary design has a higher power to weight ratio than conventional piston engines, and it can have lower maintenance costs.
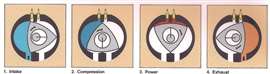
Seeking a reliable engine
In the early 1970s, with separable high-speed balanced opposed reciprocating compressors becoming the norm in upstream oil and gas applications, Ingersoll-Rand (I-R) wanted a reliable engine to drive its high-speed RDS compressors. Seeing the potential of the Wankel rotary concept, I-R signed a license agreement with Curtiss-Wright in 1972 that entitled I-R to develop, manufacture and market industrial rotary engines packaged for pumps, generators and compressors.
I-R’s objective of developing a natural gas fueled variable speed prime mover for reciprocating compressors in 500 hp (373 kW) increments at 1000 rpm involved a significant extension of the Wankel technology. I-R’s heavy duty compressor drive engine, constructed with cast iron end housings and oil-cooled, nodular iron rotors, required an engine displacement of 2500 in3 (40 L). Up to that time, the largest successful Wankel built by anyone was only 90 in3 (1.5 L).
After two years of secretive internal development, the product was formally announced at the 1976 Offshore Technology Conference (OTC) and featured in the July 1976 issue of Diesel & Gas Turbine Progress. Two 1000 rpm rotary engine models were offered, with the model numbers relating to the displacement. The IR2500, rated 500 hp (373 kW), used a single rotary module. The IR5000, rated 1000 hp (746 kW), used two rotary modules coupled together. The first unit was secretly packaged with an I-R RDS compressor at Southwest Industries and set up for no-load demonstrations after the unveiling at the OTC. I-R had a movie company secretly make a film of the whole story of the engine design, development and introduction. These were handed out along with plastic models of the engine. This big splash about a “revolutionary” new product caught the gas compression industry totally by surprise.
The compact, naturally aspirated engines had a 9:1 compression ratio. Extreme precision and surface finishes were required on the engine combustion chamber surfaces. The distinctive triangular rotor drove the output shaft through internal gearing having a 3.0 ratio. By eliminating the conventional reciprocating engine’s wearing parts and having fewer bearings and other parts, the rotary engine was forecast to have lower maintenance costs and longer service intervals.
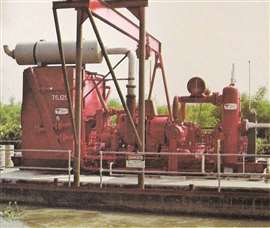
For endurance testing, an extensive field testing program was established through I-R Compression Services in Tulsa, Oklahoma. This obtained valuable field experience through leasing the rotary-driven packages for natural gas production applications. A fleet of 13 units were packaged by Southwest Industries with 1000 rpm I-R RDS compressors, and these were installed with eight different customers on one-year compression contracts that included all service provided by I-R.
Oil consumption problems
By early 1977, the lead unit had accumulated over 8000 hours, but oil consumption was economically prohibitive despite otherwise reliable operation and a respectable 32% thermal efficiency. The oil consumption was improved with a design change, however the rotor apex (aka tip) seals
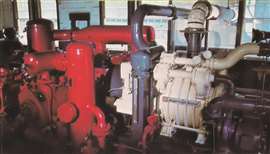
that performed very well in the laboratory, were a consistent problem when required to operate 24/7 operation in the field with natural gas fuel that varied in quality and heating value. Observers from that time humorously claimed that “the engine housings were so hot in service they would glowed brightly enough to read a newspaper by at night.” The excessive heat caused casing distortion and affected the special coatings and even the metal heat treatment of the housings and rotors.
I-R initially indicated that power modules would require change-out every 8000 hours, with the intent that this could be extended with further development. While I-R felt confident that more field development would resolve the apex seal issues, simultaneous laboratory development led to a 10% uprating of the engines, which tended to exacerbate the rotor apex seal wear that was occurring in the field.
The first customer-owned unit was an IR5000 installed at National Fuel Gas’ Heath compressor station in 1976. This was a station that was otherwise powered by reliable old Snow horizontals. Comments in a Coolspring Power Museum newsletter from that time described a field tour to the station to admire the rhythmic, comparatively quiet “chugging” horizontals. But it was interrupted by the “screaming” Wankel howling in the night.
Ultimately, 50 rotary units were placed into field applications, with 43 driving compressors and seven driving electric generators. The generator drives and 10 of the compressor drives were customer owned, with all the rest owned by I-R Compression Services. The last new unit was placed in service in late 1979, as the apex seals continued to be the engines’ Achilles’ heal.
Ultimately, the entire rotary program was a great idea that proved to be a commercial disaster for I-R. Although the company reportedly spent $10 million developing the rotary engines, which was a huge sum in the 1970s, it was said that twice as much was spent buying its way out of the product. Nevertheless, I-R lived up to its responsibility by replacing the customer owned rotary units, and presumably its own fleet units, with Waukesha gas engines.
As a side story, in the early 1970s I-R also had a conventional reciprocating gas engine through design and initial development. It reportedly looked like a good high-speed gas engine design, but the rotary won the day and the reciprocating engine never went into production.
MAGAZINE
NEWSLETTER

CONNECT WITH THE TEAM
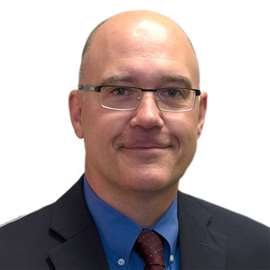
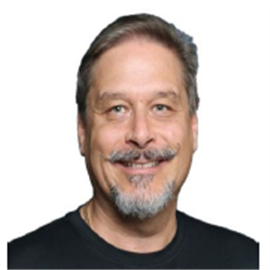
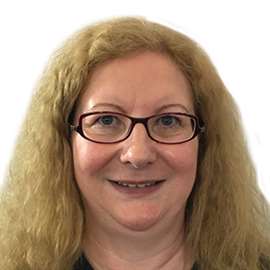
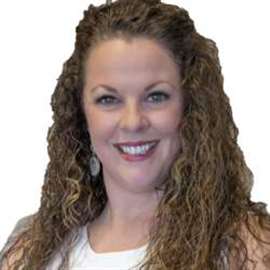