TechCorner: EFRC report provokes assessing leaks
November 16, 2020
André Eijk explores the European Forum for Reciprocating Compressors (EFRC) report that encourages the controlling of methane emissions.
With an increased global emphasis on reducing greenhouse gas emissions, notably methane and carbon dioxide, the European Forum for Reciprocating Compressors (EFRC) has made the reduction of emissions from reciprocating compressor systems one of its focus areas.
This decision prompted a comprehensive study of emissions from reciprocating compressors, including an inventory of current emissions and a review of emissions control. The resulting report,1 which is publicly available on the EFRC website covers the legal, technical and scientific aspects of emissions measurement and control, and provides a foundation for new EFRC initiatives on emissions reduction.
Methane emissions from reciprocating compressor systems are important from three separate perspectives, namely health & safety, product losses and climate change.
Emissions that threaten health & safety are likely well known to operators, but additional awareness of where these emissions occur is beneficial. Emissions that constitute lost production can often be reduced at little or no net cost, depending on the location and operating conditions.
Climate change is by far the most complex issue, but it should be clear that accurate and up-to-date knowledge of their own methane emissions is important to industry players who wish to prepare themselves for future climate-related challenges, whether these relate to public attitudes or to legislation.
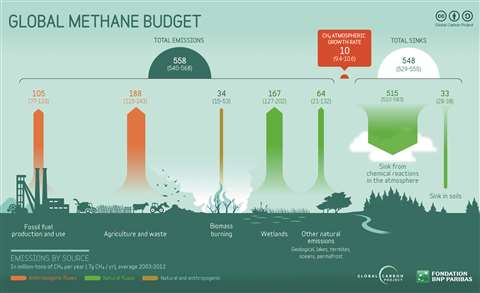
Looking for global averages
Clearly, emissions from reciprocating compressor systems will vary not just between individual machines but also across applications, industries and geographic areas. When looking at climate effects associated with methane leakage, we must also consider carbon dioxide associated with compressor drivers and the flaring of methane leaks.
Our baseline is the United States natural gas industry because it is a significant emitter of greenhouse gases and also the sector in which reciprocating compressor emissions have been studied most thoroughly. For the natural gas industry in general, emissions from reciprocating compressor systems occur at all stages – production, processing, transmission and storage.
Several studies have attempted to quantify emissions from reciprocating compressors. The 2016 Greenhouse Gas Reporting Program (GHGRP) indicates that methane emissions from reciprocating compressor systems in the U.S. natural gas industry account for 4.5 percent of total US methane emissions.
Other industries, such as chemicals and petrochemicals, have been less intensively studied, and are likely to show national and regional variations that are similar.
It is reasonable to assume that at the level of individual compressors, emissions – and the effects of emissions reduction methods – will match those from the natural gas industry, with appropriate adjustments for capacity, operating pressure and so on.
Estimates versus measurements
While reliable emission figures for reciprocating compressors across entire countries and industries are somewhat scarce, many studies offer an impression of the emission behavior of individual compressors or small groups of machines. Unfortunately, these impressions are often skewed and sometimes conflicting.
An obvious problem is the existence of “super-emitters”, such as compressor systems whose leakage is many times greater than one would normally expect. These skew the emission data and tend to create a Pareto distribution with 80% of the emissions coming from 20% of the sources.
The good news is eliminating super-emitters requires good maintenance practices, and thus both “normal” emissions and super-emitters can be targeted through similar overlapping management policies.
Looking in detail at the performance of individual reciprocating compressor systems, the literature sets out “emission factors” (EFs) for components, such as rod packings, pneumatic devices and blowdown valves. Unfortunately, these figures show such variability between studies that it is difficult to draw conclusive comparisons between different reciprocating compressor systems, and between centrifugal compressors and reciprocating compressors.
With this in mind, the natural conclusion is that operators and manufacturers wanting to quantify emissions from their reciprocating compressor systems are best off performing direct measurements on their installed equipment, rather than estimating from highly variable EFs. The high accuracy of this approach comes at a larger cost in terms of time and effort.
We can view the measurement of individual emission sources (point sources) as a bottom-up approach to quantifying emissions. The top-down approach, in contrast, relies in general on a mixture of measurements and estimates based on techniques such as:
- EFs calculated from measurements taken in other situations that hopefully are similar to the case in hand;
- background gas concentrations measured across larger areas or entire plants, and;
- mass balances.
A very good example of the impressive recent improvement of a top-down measurement system is the European Space Agency’s (ESA) Sentinel-5 Precursor (S-5P), a satellite mission focusing on global observations of atmospheric composition for air quality and climate research.
The TROPOspheric Monitoring Instrument (TROPOMI) is the payload of the S-5P mission, jointly developed by the Netherlands and ESA (scientific partners: SRON, TNO, VU; user committee: EDF, ADSN, Shell, TNO). TROPOMI considerably improves the worldwide detection and quantification of localized methane emissions, with a focus on leaks from the energy sector (oil, gas and coal).

Bottom-up measurements and top-down estimates are complementary approaches, both of which are likely to be useful in any particular situation. Estimation is cheaper and faster, while measurement is more accurate – as long as we measure the right things.
The difficulty of reconciling bottom-up and top-down figures becomes clear when we look at national and international estimates of greenhouse gas (GHG) emissions for entire industries and countries. Guidance such as the API 2009 Compendium and a wide variety of books, articles and software can help to ensure best practices when reporting GHG figures.
Several authors suggest that the best approach for a specific plant is to combine the strengths of measurement and estimation to get a reliable benchmark figure, followed by continuous monitoring to track performance over time. Various detection and measurement techniques and instruments are available, each with varying accuracies and costs.
How to reduce emissions
Estimating gas emissions is one thing, but how should we reduce them, whether for economic, safety, health or climate reasons?
Fortunately, the recip industry already has many options. Abatement methods range from straightforward techniques – periodically checking for leaks and fixing them – to technologies that improve sealing performance (Figure 3 shows an example).
It is important to keep the scope broad to consider compressor systems as well as compressors. Equipment, such as pneumatic devices and compressor drivers, provides many additional opportunities for emissions reduction.
Advice on emissions reduction methods is available from the main industry organizations and government agencies, such as the US Environmental Protection Agency (EPA). Financial pressures ensure that reduction methods are typically rated in terms of their cost-effectiveness, with payback periods ranging from several months to several years.
The good news is there is ample evidence to show that emissions can generally be reduced considerably at low costs and with rapid payback. Solutions are often quite simple, such as reducing vent losses by keeping compressors pressurized when they are stationary.

Legislation, guidance and the future
Health & safety regulations on flammable gases and volatile organic compounds (VOCs) ensure that there are already many government regulations on emissions from gas handling equipment and associated industries. Especially in Europe, this regulatory environment is becoming more stringent year by year.
However, it is also obvious that for environmental reasons, government agencies and industry professionals are recognizing the need to reduce GHG emissions, including methane.
With this in mind, the United States and the European Union have implemented equipment standards for seals, including in compressors. For example, the US EPA requires that piston rod packings be replaced every 26,000 operating hours or every 36 months.
Current moves to reduce the power of the EPA may change this situation in the future, of course. More constructively, it might make more sense to require seals to be renewed based on continuous emissions monitoring rather than time-based standards.
As industry and public awareness of gas emissions increases and legislation, in general, becomes tighter, so does the demand for related answers and methods. Many parties are stepping in to fill the gap.
Non-governmental organizations, think-tanks and semi-voluntary government programs are providing emission reduction programs, including those for reciprocating compressor systems. Some of these, at least, combine economic perspectives with their climate concerns.
Conclusion
There is already plenty of information available on emissions from reciprocating compressor systems and how to reduce them.
From the company visits associated with the EFRC report, it is also clear that many operators already know this and have started to put their own reciprocating compressor system emissions reduction programs in place. Several indicated that emissions are an important parameter during the selection process for a new compressor.
Improved piston rod packings are required to reduce or even eliminate emissions from reciprocating compressors.
In the meantime, several companies indicated that they would be very interested in safe, reliable and low-cost continuous monitoring systems, presumably using wireless communications, to measure leakage from piston rod packings.

Armed with a BSc in Mechanical Engineering, he started his career as a product specialist in gas compressors and expansion turbines for Atlas Copco in the Netherlands. He has been a task force member of the API Standard 618, API 619, API 674/675 and API 688 since 2000 and been a member of the EFRC research group since 2001.
Having worked for 40 years for TNO in the Netherlands he is a senior expert on pulsation and vibration control of pipe systems, compressors, pumps and process equipment. His lengthy track record includes being a specialist on root cause analysis of reciprocating compressor and pump systems.
He has produced several EFRC guidelines for reciprocating compressor systems that are globally used.
Eijk is a master on the finite element calculations in the area of mechanical vibrations and fluid structure interaction of compressor and pipe systems. He developed the ISO 10816-8 and ISO 20816-8 for vibration of reciprocating compressor systems and was the chairman of the standardization group of the European Forum for Reciprocating Compressors (EFRC) from 2011-2020.
MAGAZINE
NEWSLETTER

CONNECT WITH THE TEAM
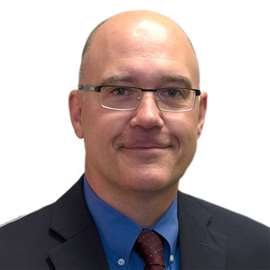
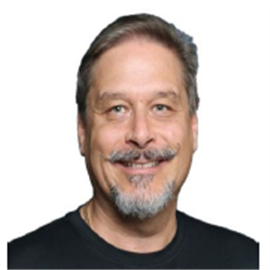
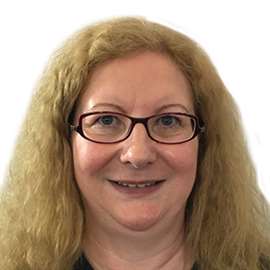
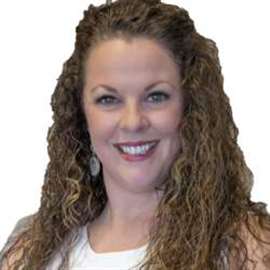