Sometimes, two drives are better than one
August 29, 2023
A Q&A with Dual Drive Technologies’ David Coker
Dual Drive Technologies, (DDT), developed a system utilizing a natural gas engine and electric driver on a single shaft coupled to a reciprocating compressor.
The ability to seamlessly transfer between drivers in less than 10 minutes, with no change in throughput, allows the end user to utilize the most optimal energy source, natural gas or electricity, with the highest profit opportunity in the market at that time. This patented design evolved into a tool that could be used for maintenance cost management, emission control, energy management, and the ability to turn an expense into revenue, according to the company.
The first compressor package was installed in East Texas in the late 1990’s and has since grown into a fleet of over 400,000 HP in multiple services from field gathering, transmission and cryogenic plant installations. Most of those are installed within Energy Transfer (ET). ET realized many years ago that Dual Drive compression was the future in many applications to meet their emission needs without adding an additional burden onto the electric grid.
Dual Drive Technologies (Dual Drive) offers a natural gas compression system featuring the combination of both a natural gas engine and an electric motor. These two drivers are both capable of individually powering the compressor.
COMPRESSORtech2 recently talked with David Coker, Energy Transfer’s vice president of Power Optimization and general manager of Dual Drive Technologies, about the technology and the market. Here is the interview, edited for length and clarity.

Q: How did the Dual Drive technology come about?
A: The founder of our company has a very good understanding of the power market and the gas market. Through his understanding of these markets, and the emissions issues our industry was facing, he realized there was a need, an opportunity, to offer a technology that will meet emission requirements while at the same time offering an opportunity to create value from energy arbitrage. The creation of dual drive compression provided this opportunity .It was the first compression technology that reduced emissionswhile at the same time being able to be optimized between natural gas and electricity. So, even though it helps accomplish emission reduction goals it really is an optimization tool In 2009, we officially became a part of Energy Transfer.
Q: Was that a tough sell in the marketplace? No one wants to be first, no one wants to get product number 001 in their compressor station.
A: Well, it was a very tough sell—it was one of the hardest things I’ve ever been a part of. With that said, by the time I became a part of DDT it had been in operation for many years, so many of the hard days were behind us. For the earliest days, when starting a company like that, and it’s a brand new technology, and going through those phases of creating and introducing something new, there’s a lot of pain associated with that. Truly understanding cross-commodity optimization and energy management is a difficult deal for many people, in order to explain energy management, you really do have to understand the language. And so DDT had the growing pains of a new piece of mechanical equipment that required learning how to operate and maintianwhile at the same time dealing in a market that had no understanding on the product at all; not an enviable position to be in. But 2009 was the year that DDT came into the Energy Transfer Partnership and really started making some big transitions. The original design system was completely different with a compressor in the middle and an engine and motor on opposite ends. In late 2009 or early 2010, We made a trip to Ariel Compressors in Mt. Vernon, Ohio, for the purpose of designing a through shaft compressor so that we could have an Ariel compressor in the middle, but before we left we had decided on a new plan to put the piece of equipment that requires the least maintenance, the electric motor, in the middle. That idea seems like a no-brainer now, but at that time there had been a lot of effort to make the original design work and it was working. By having the motor in the middle a standard compressor—an Ariel compressor— could be used so we changed our package to a Cat-Ariel package. So, we have our current configuration with an engine on one end, an electric motor in the middle, and then an Ariel compressor at the other end. And that was kind of the big move that we made in order to make DD compressors more familiar to people in the field, especially for project engineers. But you hit the nail on the head when you asked if it was a tough sale…If you’re a manager on a project, and you install a straight Cat gas engine driven compressor and it doesn’t run, then you did the best thing you can do and it is up to the commissioning folks to make it run. If you’re the project manager and you make the decision to switch over to Dual Drive, and it doesn’t run then you may have to look for a new job. So, we really had to get some traction by proving our technology and we have taken great strides in doing that and have gotten a lot of traction. One of the most important things to understand when trying to sell a DD is knowing the market and knowing where the Dual Drive fits, and it doesn’t fit in all places. But when people see that it’s a successful piece of equipment, that it’s the one of the most reliable compressor packages available, and we have proven that,. people start warming up to it.
Q: What interests operators in the system?
A: Initially, people are going to be looking at it from an emissions reduction perspective. One of the easiest things to do if you’re in the gas business, is to install natural gas compression because natural gas compression is something that is understood and has always been relied upon by the gas business. Obviously, in our current environment, there’s a big problem with that. and that is dealing with emissions and the permitting that goes along with it. So, if there is a solution that offers the benefit of emission reduction, but offers that benefit without having to solely rely on an electric motor, by giving an option to fall back on that you are comfortable with, a gas engine,. On the other side, a lot of people never think about the energy management, so that kind of becomes cream off the top. In the right locations, Dual Drive is the only compressor that will pay for itself with something other than throughput, and that is energy management. Even though this is something we have been doing for a long time, for many it seems like a new technology and we need to change that thinking.
Q: Talk about the applications? Where is it best suited?
A: Currently, every DD compressor operating is in Texas. They are in both the ERCOT deregulated power market and and cooperative markets. Some cooperative power marketsare really great places to replace straight electric drive compressors. The energy management benefits in those areas can be accomplished with minimal runtime on the gas engines, possibly as little as 150 hours of engine run time in the ERCOT deregulated market, there is a requirement to identify arbitrage opportunities between natural gas and power as well as participation in the ERCOT ancillary service market. In both regulated cooperative markets and the ERCOT deregulated market there is the opportunity to avoid the 4CP demand charges by transferring to gas over the summer peaks. As far as the application goes, the DD is a fit for gathering, processing, and transmission compression applications.
Q: So you’ve got to be working very closely with the operators to figure out if you’re going to be the right solution for them.
A: Yes. Every single day, we have an internal meeting at 8:30 a.m. to strategize how we will manage the same day market as well as the next day. Once those decisions are made, emails are sent to has all Dual Drive locations giving DD operating instructions for that day, and what the plan is for the next day. We are not in the business of just selling aa compressor and leaving it up to the customer to figure out the market. We want the customer to be successful with DD, so our energy management instructions are to help them accomplish that. This summer ERCOT has seen extremely high peak loads that have broken 85,000 MW, something that seemed impossible just a couple of years ago, and through our energy management program we have kept people informed of expected 4CP days as well as potential tight capacity days that could cause ERCOT real-time prices to go extremely high. On these days, we send out e-mails telling operators that they need to transfer to gas engine for the hours of noon – 8:00 p.m.; the range of time can vary according to the day. It is then up to the operator to choose to execute the transfer.
Q: It sounds like the goal of Dual Drive is really about optimization for when it’s going to be running on either engine or electricity. And it’s going to be always available no matter what, basically.
A: You don’t want to give a false perception that if you lose power a gas engine will always run, for most applications a backup generator is needed that is large enough to keep the gas engine controls energized.. A great example is (winter storm) Uri. Every plant that was able to continue running because it had power was able to provide enough gas to operate the DD compressor. During Uri, Dual Drives were transferred to gas engine. When the grid is in crisis mode and the price of power is at their caps, during Uri that was $9,000/Mw, and a 5000 HPDD compressor was transferred from motor to gas engine, that is 3.73 MW removed from the grid. In a Uri situation, 3.73 MW is a huge impact, from both a financial and grid security perspective. If we multiply that by a large number 5,000 HP compressors that could be a grid saving impact.
Q: How quick is the switchover?
A: Because of the ERCOT requirements to participate in ERCOT Demand Response programs, our DD units transfer from motor to engine in under 10 minutes and most are programmed to do so in as little as 7 minutes, With the load resource program with ERCOT, there is only 10-minute window to be in compliance. So, the units receive a signal and automatically go into the transfer mode during a Load Resource deployment by ERCOT. In those situations, you really must take human interaction out of it, the DD automatically starts transferring when ERCOT deploys load resources. If you’re going from gas engine to electric motor, it’s almost instantaneous.
Q: So what about outside of Texas? Are there plans to move to other areas, other plays?
A: We’ve got two of them that just went through a test run on the shop floor and are being installed up North on a transmission line for a third party. In order to reach more customers we have developed two different contractual agreements for customers who are interested in DD compression We have an energy management agreement and a licensing agreement so people can pay for a license and manage it themselves. With a licensing agreement, the customer can install it anywhere, and operate it the way they want to. If they desired, the licensee could hire DD to perform energy management, or if they chose to perform those activities themselves, they could.
Q: So it’s still the same philosophy in this other market?
A: Anywhere a DD is installed there has to be of being capable of transferring form one drive to the other. That benefit could be financial benefits or they could be the benefits of having a gas engine to transfer to on an unstable electric grid. As we see the continued development of renewable energy there will be a greater need of having load shedding capabilities for both financial and reliability reasons. Something that happened after Uri was that ERCOT passed a rule called NPRR 1087. The original language in the rule prohibited any critical natural gas infrastructure from participating in the ERCOT ancillary service market. This rule passed for the obvious reason that critical infrastructure needs to continue operating in a Uri situation, but something that ERCOT needs is for more people to participate in ancillary service markets to be able to shed load during those moments. We were able to get an audience with the authors of that rule and were able to demonstrate for them our transfer from electric to gas and how there’s no change in throughput. at the final language of NPRR 1087, prohibits critical natural gas infrastructure from participating in any ERCOT ancillary service markets unless they have 100% backup generation or another type of technology they can transfer without a change in throughput. As far as I know, DD is that technology.
Q: Do you see growth in areas outside of Texas like this?
A: Absolutely. The previous area outside of Texas is a transmission pipeline and we have additional regulations like the Good Neighbor rule and others that are constantly making it more difficult to do business in the market that we’re in. Because of these regulations, companies are having to replace old compressors that produce high emissionswith newer technology. Without the option of Dual Drive compression the next best option is straight electric driven and straight electric isn’t a great option just isn’t really a great option because of the grid situation we are dealing with nationwide and the cost risk of being held captive to the electricity market. Dual Drive Technologies only sells DD compressors but there is an opportunity to lease DD compressors from USA Compression.M Dual Drive offers the best of both worlds, emission reductions and cost reduction through energy management.
MAGAZINE
NEWSLETTER

CONNECT WITH THE TEAM
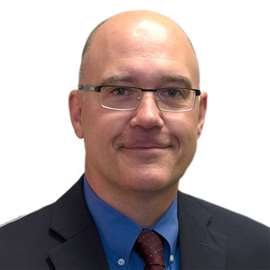
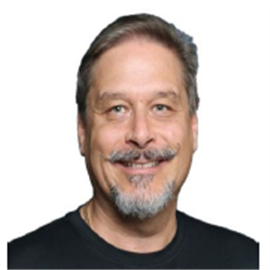
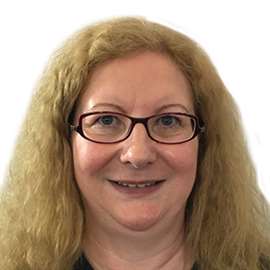
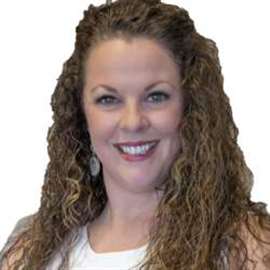