Smart packing
July 03, 2020
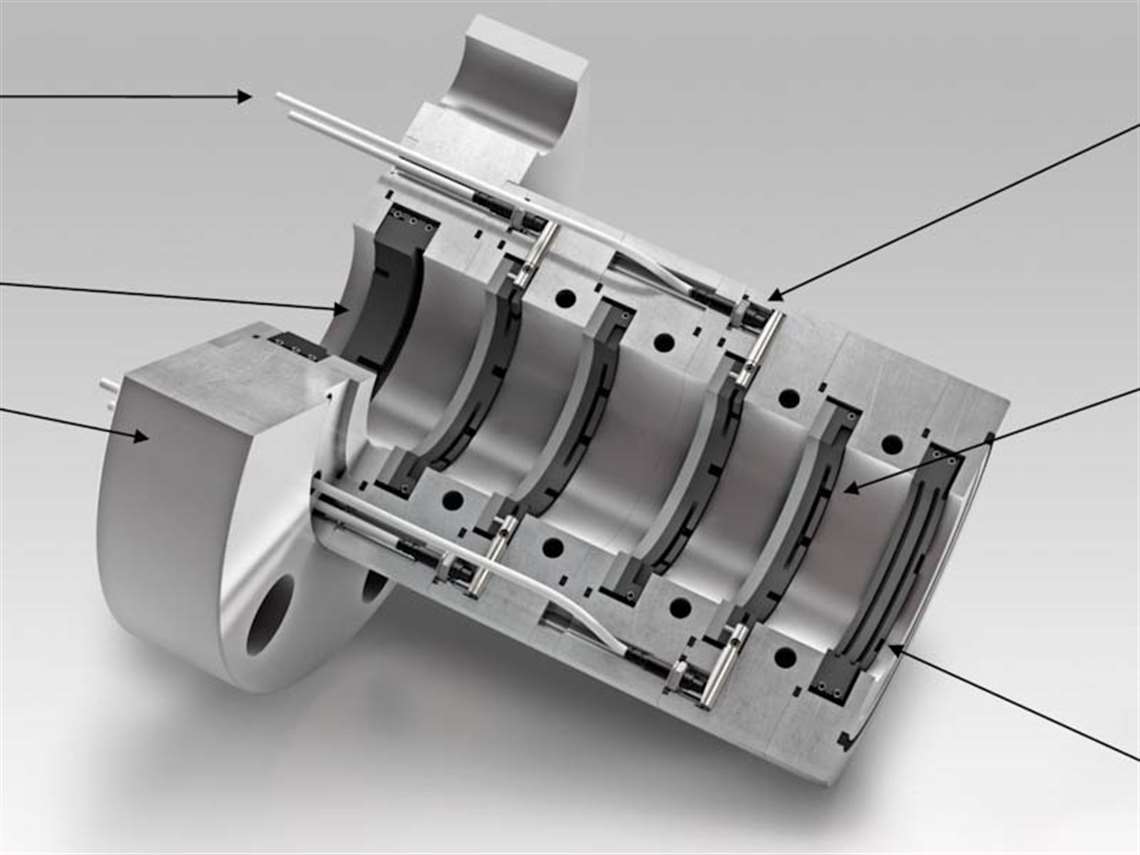
STASSKOL device designed to monitor wear, status of piston rod packing sealing elements
AUTHOR’S CORNER: Marc Langela is the head of material and product development for STASSKOL. He joined STASSKOL in 2007 as the head of the research and development department. He is responsible for developing new sealing materials and new spare part designs, as well as improving technical processes and workshop standards. Prior to STASSKOL, Langela developed customized polymer materials for various technical applications at a company in Bavaria.
Editor’s Note: Langela presented this paper in September 2019 at the 4th International Rotating Equipment Conference in Wiesbaden, Germany.
Introduction
Reciprocating compressors are widely used to compress gaseous media for industrial applications, such as at chemical plants for hydrogenation reactions, polymerizations or Polysilicon productions. These are fully-integrated and automated industrial processes, which are running continuously. A failure in compressor operation can cause unexpected and expensive downtime.
In consequence, reliability is one of the most important properties of reciprocating compressor systems. The crucial items in respect to reliability are often the spare parts of the bare compressor. According to a study performed by Dresser-Rand, piston rod packing are the second most common cause of failure (Figure 1).
The materials of the sealing elements are tuned for longevity, but optimization has its limits. Negative influences like gas impurities and process variations can lead to increased wear and reduced reliability. Even the best material and design cannot guarantee sufficient operation at a high level.
In consequence, a solution to monitor the wear status of the sealing elements of a piston rod packing is needed to achieve the best reliability of the system and to utilize the maximum running hours of the sealing elements.
Up to date solutions
Currently, the industry tries to estimate the wear status of the piston rod packing internals by:
a) measuring the temperature at the vent line
b) measuring the leakage gas flow
c) measuring the temperature within the
pressure packing.
Read the rest of the story here.
This article was originally published in the January-February 2020 issue of COMPRESSORTECH2. We only publish a fraction of our magazine content online, so for more great content, get every issue in your inbox/mailbox and access to our digital archives with a free subscription. Click here for a new subscription or here to renew your current subscription.
MAGAZINE
NEWSLETTER

CONNECT WITH THE TEAM
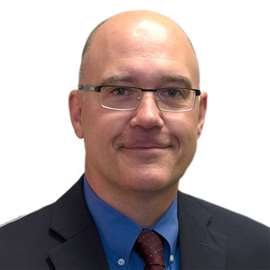
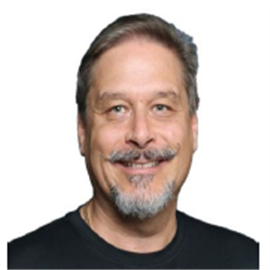
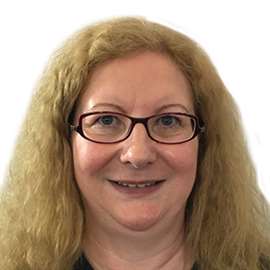
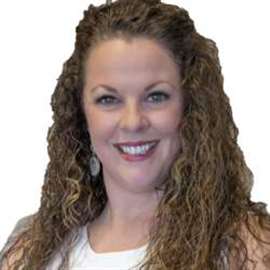