Sloan updates lubrication system
February 03, 2022

In a world where many consider more to be better, engineers know this is not always the case. Lubrication systems on high-speed compressors can overlubricate, a problem which results in carbon buildup, excessive emissions, catalyst fouling and downstream pipeline contamination.
Under lubrication is separate problem, causing components to wear more quickly. Both problems, if left unchecked, can result in downtime and expensive repairs.
For compressors that operate at a steady state, maintaining proper lubrication is not a problem. The unit needs a specified amount of lubrication at given intervals and the lubrication system is designed to provide exactly that amount. But many applications in the energy industry require variable power, which results in changing lubrication needs over time.
Sloan Lubrication Systems recently added new capabilities to its advanced lubrication system that automatically index lubrication rates to variable conditions. The system, known as TriCip, is designed to index lubrication rates to brake mean effective pressure (or BMEP) for lean burn, two-stroke engines.
“Our goal is always to maintain sufficient lubrication. Our direction on indexing lube rates is to follow the OEM recommendations and follow our standard parameters based on the horsepower,” said Bryan Boarts, Sloan project manager and sales engineer.
In most cases, traditional lubrication systems are manually adjusted. An operator generally needs to physically adjust pumps one at a time to achieve the correct flow rate. However, it is often not practical to make these physical adjustments each time operating conditions change, he said.
Some traditional lubrication systems are driven by an auxiliary shaft and do vary to a degree with changes in RPM. However, the relationship between shaft rotation and lubrication requirements is not 1:1, so these systems do not provide the correct flow rate under variable conditions either. In addition, they are not capable of accounting for changes in BMEP due to fluctuations is gas composition, he said.
Sloan’s TriCip uses an advanced control and monitoring system that can change the lubrication flow rates to match the needs of the power cylinders as conditions change. This is a capability unique to TriCip.
When a significant reduction in BMEP or RPM is required, TriCip has a variable speed motor to ensure the compressor and engines hit the target lubricant flow rate. “Without a variable speed motor drive, can’t do that,” Boarts said.
TriCip was originally designed with compressor cylinder lubrication in mind. TriCip combines a proprietary lubricant with a state of the art lubrication system and advanced iiot monitoring and control to enable up to a 90% reduction in required compressor cylinder lubricant.
One TriCip unit can replace the lubrication system on all throws of a reciprocating compressor. A compressor station with multiple compressors would take a TriCip system for each. The TriCip system was introduced in 2018 and hundreds are in operation today, he said. “We want to continually deliver a small amount of lubricant often rather than dumping a large amount of lubricant at one time,” said Eric Sloan, manager of marketing communications at Sloan lubrication.
The result is a significant reduction in oil delivered to both the engine and the compressor system. The reduction in oil allows the engine to reduce emissions, improves uptime and reduces carbon buildup.
When an end user can reduce the oil user by almost 90% over an entire pipeine system, the savings are significant, not just in terms of cost but also in the reduction of the problems caused by excessive oil carryover, Sloan said.
Excess oil carryover can foul the pipeline, sensors and metering stations downstream from a compressor station and damage customer equipment like power turbines. Ultimately, that contamination has to be removed through pigging, an expensive and environmentally challenging process.
To retrofit an existing unit, Sloan technicians spend a day or two on pre-work, working on the tubing while the unit stays in service. Once the pre-work is finished, the operator will shut down the unit and the technicians will install the system, complete the tubing connections, replace the check valves and then proceed with the commissioning checks. That can take another two days.
The TriCip fluid is a specially formulated fluid for gas compression that is delivered in 20 liter bag-in-box packages, which are loaded directly into the TriCip delivery system. “We have not had any issues with units dispensing too much oil, and the BIB system simplifies the lubricant supply chain,” Boarts said.
The delivery system has an accessible user interface that is easy to monitor. Each cartridge can last 10 to 40 days, depending on the run rates and needed lubrication.
TriCip can be used with compressors made by Ingersoll Rand, Cooper Bessemer, Clark and Ariel/Superior. Sloan’s key customers are interstate transmission pipeline operators, and particularly gas compression, but they also serve a wide range of other industries.
“Want to help customers meet goals, which goes beyond a single lubrication system or a single compressor package,” Sloan said. “The majors are talking about a massive energy transition over the next 15 years. How do they, in the short run, do whatever they can to minimize their impact while maintaining their productivity and profitability? By drastically reducing the lubricant consumed by compression operations, TriCip can make a meaningful positive impact while improving their bottom line.”
MAGAZINE
NEWSLETTER

CONNECT WITH THE TEAM
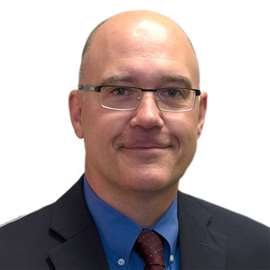
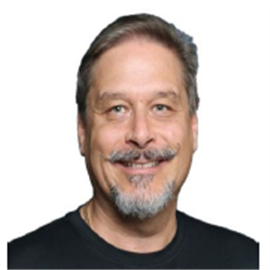
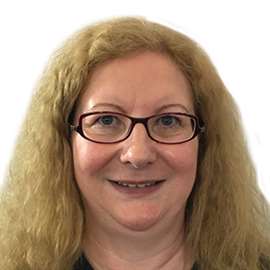
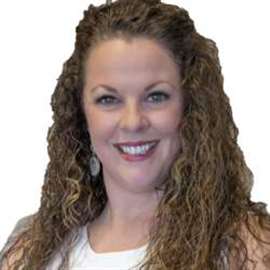