Sloan celebrates 100 years
October 25, 2022
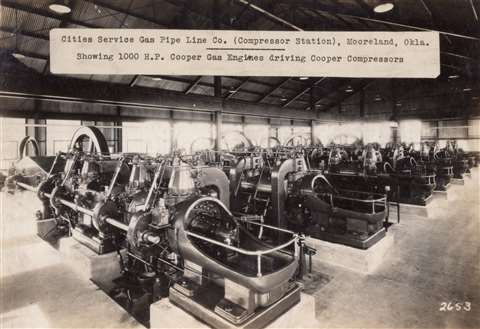
A century of operation is a long time. Sloan Lubrication Systems has not just survived, but has thrived for that length of time because of its ability to recognize customer needs and provide a solution for them with reliable and innovative products.
The company dates back to 1922, when brothers Ralph, Paul and Walter Sloan founded the company in Pittsburgh, Pennsylvania with an initial focus on mechanical lubricators used in heavy industry, steam-to-water heat exchangers and steam traps.
Walter’s son, John, joined the company after his service in World War II and became the second generation of the Sloan family to push the business forward and adapt to changing times. He helped the business transition to provide accurate, protected lubrication systems for the natural gas transmission industry.
In 1972 the focus shifted again as Walter Sloan II joined the firm. He was the son of John Sloan and the third generation of the family to run the company. Soon his brother Andrew and sister Nancy joined and implemented new technological developments in lubrication systems for compressor applications in natural gas, refining, chemicals and emerging industries. Some of the innovations included the installation of some of the first divider block lubrication systems which are still industry standard today.
In 2003, Walter’s son, C.J. joined and brothers Brian and Eric followed in 2008. The brothers were the fourth Sloan generation invested in the constant development and innovation of lubrication technology, while continuing to maintain Sloan Lubrication’s dedication to customer satisfaction.
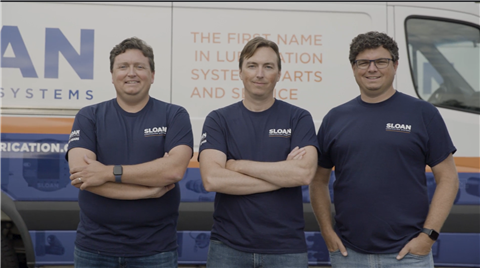
In 2008, Sloan Lubrication Systems moved Oakmont PA to a new 30,000 sq ft facility in Freeport Pennsylvania and later expanded internal manufacturing capabilities to ensure delivery of the highest quality Lubrication Systems for customers who have come to expect superior performance.
Today the company provides lubrication systems for industrial equipment and is a supplier and distributor of Ariel components. The bulk of its business comes from oil and gas, although it continues to serve other industries.
Brian Sloan, CEO, said that after a century of operation, the company knows its customers well and understands essential business needs. “The reason we’ve been around for 100 years is that we deliver reliability,” he said. “The customer has a need for reliable products and we are fortunately in a position to make and designs those products in house.”
He added that the benefit the company provides to the customer comes from the combination of its reliable products and its top-notch field service capabilities.
After a century in operation the company has seen some long-term trends hold constant and some fundamental changes in the last few years. For one, customers heavily concerned about the environmental impact of their operations.
“This presents huge opportunities for us,” said Steve Spotts, Sloan’s VP of sales. “We are Sloan recognize this and are working to help our customers meet that need.”
Key product
One of the company’s products, TriCip, was designed for compressors and their engines to reduces waste, improve efficiency and boost reliability. “The system allows them to move more gas efficiently and lower their carbon footprint,” said CJ Sloan, the company’s chief technology officer.
TriCip is one of the products that the company developed after consulting with customers about the need for reliability, longevity of assets and to solve the pervasive problem of lube oil carryover from compression. TriCip is an advanced lubrication system the company first introduced in 2018 that utilizes a special lubricant for compressor cylinders and optimizes rates from an existing crank case supply for power cylinders. One TriCip unit can replace the lubrication system on all throws of a reciprocating compressor. A compressor station with multiple compressors would take a TriCip system for each.
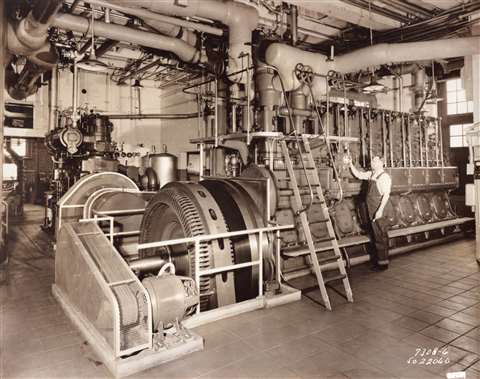
The system is designed to require up to 90% less lubricant, keeping key components properly lubricated without overlubricating. Hundreds of the units are in operation throughout the oil and gas industry. The end result is a significant reduction in oil delivered to the engine and the compressor cylinders.
When an end user can reduce the oil used by almost 90% over an entire pipeline system, the savings are significant, not just in terms of cost but also in the reduction of the problems caused by excessive oil carryover, Sloan said.
Excess oil carryover can foul the pipeline, sensors and metering stations downstream from a compressor station and damage customer equipment like power turbines. Ultimately, that contamination has to be removed through pigging, an expensive and environmentally challenging process.
Sloan Lubrication Systems recently updated its TriCip system to automatically index lubrication rates to brake mean effective power (BMEP.) Sloan’s TriCip uses an advanced control and monitoring system that can change the lubrication flow rates to match the needs of the power cylinders as conditions change. This is a capability unique to TriCip and Sloan’s updated Watchman System.
The power-side benefits of the reduction in lubricant are reduced engine emissions, improved uptime, reduced carbon buildup and less fouling of engine exhaust and catalyst systems.
“Our goal is always to maintain sufficient lubrication. Our direction on indexing lube rates is to follow the OEM recommendations and follow our standard parameters based on the horsepower,” said Bryan Boarts, Sloan regional representative covering the Eastern US.
When a significant reduction in BMEP or RPM is required, TriCip has a variable speed motor to ensure the compressor and engines hit the target lubricant flow rate. “Without a variable speed motor drive, can’t do that,” Boarts said.
Solutions provider
Even after a century in operation, the company remains a family-owned business, which enables it to respond quickly to customer needs. The company makes its products from the ground up and delivers them to customers.
“This allows us to respond to our customers a lot faster than others,” said CJ Sloan, Chief Technology Officer.
One trait that has enabled the company to grow over 100 years is the ability to listen to a customer, understand core business needs and provide a solution to meet those needs, said Eric Sloan, director of marketing.
“We don’t just sell parts and a service. We sell solutions,” he said.
MAGAZINE
NEWSLETTER

CONNECT WITH THE TEAM
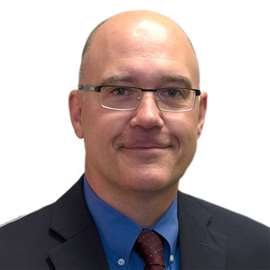
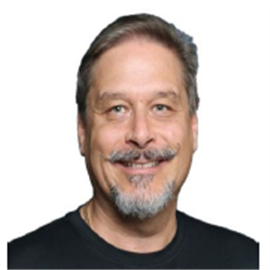
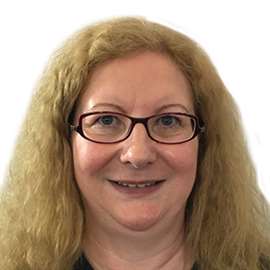
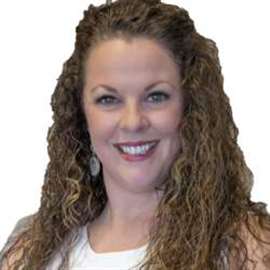