Plug-And-Play compressor valve repair
November 28, 2023
Simplified field maintenance
The expression “plug and play” originated with the computer industry. It describes a device, such as a printer or monitor, that only needs to be connected to work perfectly. No configuration, adapters, or any other actions are needed.
Over time, the meaning of plug and play broadened to describe a wider range of things, from a kitchen appliance that works right out of the box to a new hire who requires no training to perform his or her duties. The basic concept is the same – you add or replace something and it simply works.
Now apply the concept of plug and play to equipment maintenance – specifically compressor valve refurbishment – and you create an entirely new and substantially better paradigm for routine valve service. That is one of the design principles behind the StraightFlo reciprocating gas compressor valve from Zahroof Valves Inc. (ZVI).
A ‘Disruptive’ Design
In 2014, ZVI commercially introduced the StraightFlo compressor valve as a direct replacement for traditional OEM valves. Among the advances of its patented design is the ability to disrupt conventional valve maintenance, the company said. With a design that includes modular reed sealing elements and a straight gas flow path through the valve, it is designed to eliminate both conventional valve repair and the need for complete valve assembly replacement.
“With a StraightFlo valve, normal wear is contained in replaceable modules,” said ZVI CEO James Ilaria. “There is zero wear and tear on the metal valve housings because they never contact moving parts.
“This is a completely different approach from traditional valve designs where the metal seats and guards suffer wear from repeated high-velocity impacts by the sealing elements as the valves open and close. These valves often require machining at offsite machine shops before they can be returned to service. For some profiled ring and plate valves, machining procedures are extremely precise and can only be done by certified service providers with CNC machining equipment.
“Furthermore, traditional seats and guards can only be machined a limited number of times before they reach minimum thickness and must be scrapped and replaced with new ones,” said Ilaria. “At ZVI, we refer to this as ‘The Repair & Replace Hamster Wheel.’ These costs add up over time and drain OpEx budgets.
“Compare that to StraightFlo housings, which typically last the life of the valve. In fact, ZVI offers a 10-year warranty on valve housings.
As for the modules themselves, each is a specialized component with a metallic reed to control the flow of gas, Ilaria said. Modules are standardized in size so the same part can be used in various valve sizes (larger valves simply have more modules) and in many different compressors.
“For compressor operators, especially those with large and diverse equipment fleets, this part versatility can drastically reduce the number of parts in inventory when compared to stocking complete spare valve sets and repair kits,” Ilaria said. “Controllers and finance professionals know all too well how excessive working capital can be tied up in spare valves. With StraightFlo valves, operators only inventory spare modules.”
Field Repair
Modular reed design also enables a streamlined repair procedure that can be performed entirely at the compressor location, the company said.
“When StraightFlo valves need service, a technician opens the valve, replaces worn modules with new ones - by hand and with no special tools - and then reinstalls the valve without ever having to leave the compressor deck,” said Ilaria. “The valve is completely restored and ready to operate in about 10 to 15 minutes.”
“Think about how this plug-and-play method of valve repair saves time and money by eliminating the need for spare valve assemblies, vast inventories of replacement parts, off-site machining, pressure testing, special tools, and extensive training of technicians to master valve repair.”
Ilaria noted that replacement modules can be carried in a container the size of a shoe box for one compressor or a small file cabinet for multiple installations. Only three to four different module configurations are needed to cover an entire compressor station, refinery, or offshore platform – irrespective of compressor size and compressor brand. ZVI customers say their inventory carrying costs are reduced by up to 80% versus traditional valve maintenance. Logistics are also simpler compared with the effort required to maintain and distribute large numbers of spare parts.
“The savings in time, money, and resources only multiply when this concept is applied fleet-wide. And for hard-to-reach locations like remote pipeline compressor stations or compressors on offshore platforms, plug-and-play field repairability is a game-changer.”
Methane Intensity
Although a key advantage, field serviceability is just one part of the demands placed on today’s compressor valves, the company said.
“A valve you can service in the field is great. But a valve that rarely needs service at all is better,” said Ilaria. “The straight-flow design performs extremely well in gases with entrained liquids and solid particles. The reed valve tends to be self-cleaning as the flow carries contaminants through the valve. This is unlike traditional valves, where the gas flow directly impacts the sealing elements, often leading to valve failures and debris build-up in the low-velocity regions of the flow passages.
“The same dynamic affects valve efficiency,” said Ilaria. “In traditional valves, the gas flowing through the inlet valve ports directly impacts spring-actuated polymer plates, concentric rings, or poppets. Gas is then redirected multiple times before it exits through outlet valve ports. This flow redirection creates a tortuous path for gas and a significant pressure drop across the valve. As the name implies, gas flowing through a StraightFlo valve opens metallic reeds and proceeds unobstructed, resulting in lower pressure drop and improved efficiency. We apply those efficiency gains by custom-engineering modules to meet each customer’s objectives. That may be taking advantage of opportunities for increased throughput or reducing the power needed to drive the compressor.”
Governmental regulations, corporate decarbonization initiatives, and increasing scrutiny from investors, consumers, and environmentalists make emissions reduction an ever-present concern as well. “Approximately 36% of all unscheduled reciprocating compressor shutdowns are due to valve failures,” said Ilaria. “Each shutdown for valve repair or replacement requires blowdown and purging of the compressor and associated piping, sometimes resulting in venting or flaring substantial volumes of gas. The StraightFlo design makes the valves intrinsically more reliable than conventional valves, increasing the Mean Time Between Failure (MTBF) of the compressor due to valve issues from 2X up to 35X and eliminating a significant number of gas release events.”
Widespread Application
ZVI’s StraightFlo valves are widely used by major players throughout the energy industry. In upstream oil and gas, they are used in gas gathering, gas lift, and CO2 injection for enhanced oil recovery, as well as compression applications for offshore rigs. In the midstream, StraightFlo valves are found in natural gas processing plants, pipelines, and storage facilities. Downstream applications include oil refineries and chemical facilities in applications with hydrogen, nitrogen, ethylene, propane, and butane mix gases.
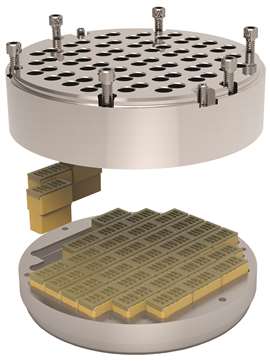
“With advantages in field repairability, as well as reliability, efficiency, power consumption, emission reduction, and reduced repair and inventory costs, the total life cycle value of StraightFlo valves is extremely compelling for reciprocating compressor owners,” said Ilaria. “Our customers see payback periods ranging from two weeks to three months depending on the application. With the recent launch of our lower-cost StraightFlo SE valve with 4140 steel housings, upstream and mid-stream operators now have every incentive to consider ZVI valves fleet-wide.”
MAGAZINE
NEWSLETTER

CONNECT WITH THE TEAM
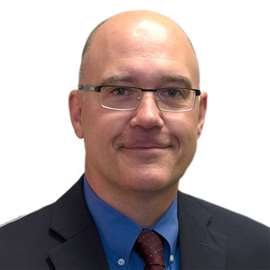
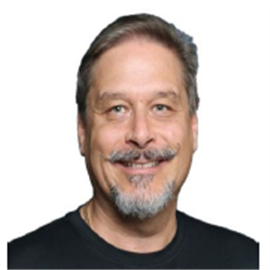
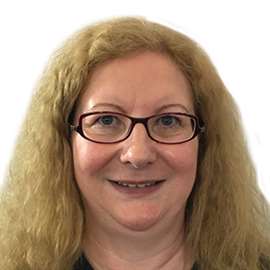
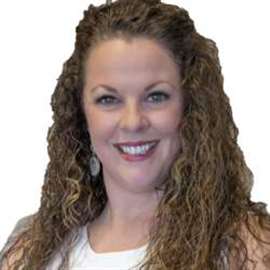