Neuman & Esser: Storing hydrogen
July 23, 2025
Hydrogen storage is heating up — and Neuman & Esser is building the compressors to handle It.
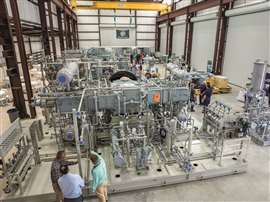
When it comes to industrial compression technology, Neuman & Esser (NEA) isn’t thinking small. At a recent industry event, Joseph Lesak, Sales Manager at NEA, painted a compelling picture of how the energy landscape is shifting — and how compression technology is evolving to meet those changes.
Lesak made his remarks at Neuman & Esser’s Customer Day event at its Katy Production Center. Company experts provided technology updates, offered a tour of hydrogen electrolyzers and compressors in production as well as a visit to Custom Heliarc’s new packaging facility in Brookshire, Texas.
Bigger compressors for a bigger energy challenge
The focus of Lesak’s talk was a massive hydrogen storage project in Europe — one driven by the geopolitical upheaval of recent years. With the war in Ukraine disrupting the continent’s access to Russian natural gas, European countries have been forced to rethink their energy strategies. One emerging solution: large-scale hydrogen storage.
Hydrogen, long considered a promising but complex energy carrier, is now moving from concept to reality. And storing it safely, efficiently, and at scale requires compressors unlike any currently in operation.
Lesak explained how this new project involves installing four enormous, foundation-mounted reciprocating compressors — each driven by a staggering 25,000-horsepower motor. These aren’t the compact packaged systems often seen in industrial plants. These are custom-engineered, high-pressure, high-capacity machines, purpose-built to inject and withdraw hydrogen from underground storage caverns.
A new set of technical challenges
Moving hydrogen isn’t like moving natural gas. Lesak emphasized that while the gas itself is simpler (pure hydrogen is easier to model than complex gas mixes), the operational challenges are far greater.
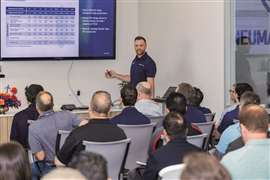
Hydrogen requires a compressor system that can manage extremely broad pressure and flow ranges, often within a single duty cycle. That makes the reciprocating (or “recip”) compressor a smart choice — especially one with what Lesak called “rubber band” flexibility, able to stretch between high and low loads seamlessly.
Beyond performance, safety is paramount. Hydrogen is highly prone to leakage, and its small molecular size makes it harder to contain. NEA’s compressors for this project feature specialized static packing that seals the machine once it stops, minimizing fugitive emissions. There are also extensive pulsation and piping studies involved to ensure system integrity under fluctuating loads.
Efficiency that matters
One standout statistic Lesak shared: these compressors achieve 97% adiabatic efficiency when storing and withdrawing hydrogen — a level of performance that helps make hydrogen a more commercially viable energy option.
Why does this matter? Because hydrogen remains expensive compared to other fuels, and efficiency gains like this help drive down the overall cost of storage and distribution.
Engineering for the unknown
Perhaps the most intriguing aspect of this project is its experimental nature. Lesak acknowledged that starting and stopping machines of this size — especially when running intermittently based on hydrogen supply and demand — is largely uncharted territory.
Europe is under pressure to innovate, and projects like this are breaking new ground in energy infrastructure. As Lesak put it, while the U.S. still enjoys a relatively stable natural gas market, European nations are urgently testing new technologies, hoping to build a reliable, renewable-driven grid backed by large-scale hydrogen storage.
More than a compressor
Lesak closed with a message for engineers and project managers: in hydrogen projects, the compressor is just one piece of a highly complex puzzle. Piping design, safety systems, control schemes, and adherence to industry standards like API 618 are just as critical.
His advice? Treat these standards like a bible — they’re written from the lessons learned on projects just like this.
MAGAZINE
NEWSLETTER

CONNECT WITH THE TEAM
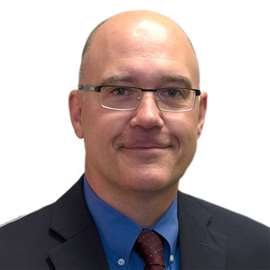
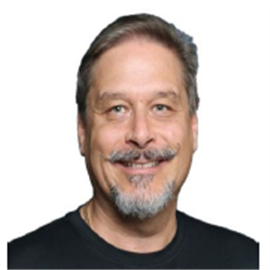
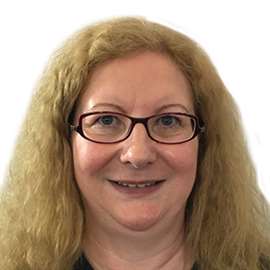
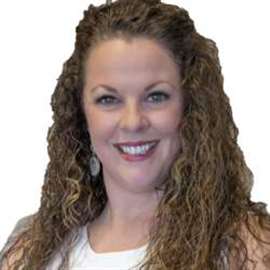