NEA Goes Bigger Into Midstream
December 11, 2017
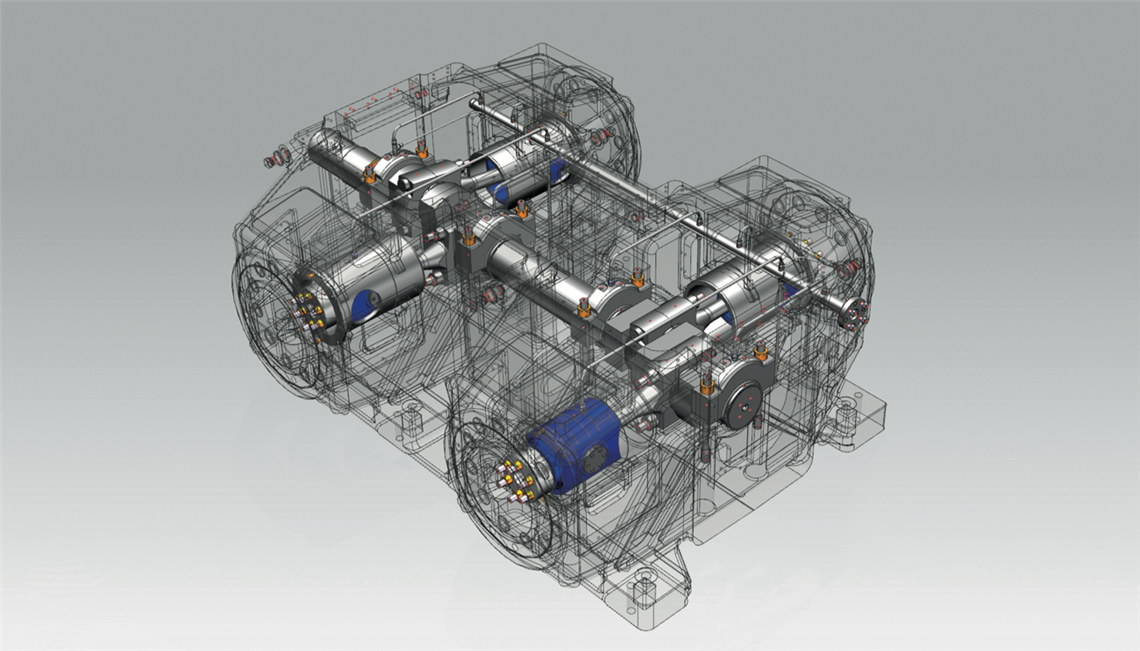
This article was originally published in the October issue of COMPRESSORtech2. We only publish a fraction of our magazine content online, so for more great content, get every issue in your inbox/mailbox and access to our digital archives with a free subscription.
Neuman & Esser Group (NEA) introduced a high-speed compressor frame optimized for midstream service: the 560hs.
The two-, four or six-throw 560hs has a 6.9 in. (175 mm) stroke, 126,000 lb. (57,000 kg) rod load and runs at 600 to 1200 rpm. The compressor is rated up to 10,000 bhp (7456 kw) and up to 15,000 psi (1034 bar) and has been optimized for 600 to 1200 rpm large gas engines or electric motors.
Primary midstream applications for the 560hs high-speed model are gas storage, gas gathering, pipeline, gas boosting and all technical gases.
NEA said the development of the 560hs was driven by customer feedback and requests. NEA began its foray into high-speed frame compressors in 2000 with the 320hs. The 320hs was for the natural gas storage market, but the frame has been utilized in gas boosting, industrial gas generation, gas pipelines and various residues and hydrocarbon gas mixes. Since 2011, NEA has been present in the North American midstream compression market with major orders for various natural gas and CO2 for enhanced oil recovery applications. The company optimized the compressor line to utilize the high-speed capability available of its portfolio.
“NEA frames were already available with a large range of strokes, and the flexibility offered a good fit for engine drive applications,” said Andreas Hirschter, head of Strategic Marketing at NEA.

According to Joseph Lesak, key account manager, Neuman & Esser USA Inc. in Katy, Texas, customers recognized the flexibility of NEA’s compression portfolio and started questioning why NEA didn’t just go ahead and make a new frame designed specifically for larger midstream applications.
After studying the larger engine-drive applications and gaining more feedback from customers, the NEA’s Central Division of Technology decided to design a new optimized frame for the midstream service: the 560hs.
“The team decided on the need for a compact compressor but with high rod load capabilities to pair easily with the larger engines of this industry,” Lesak said. “The decision was taken to utilize the crankshaft, main bearings, crosshead and piston rod derived from an existing and proven API 618 running gear to handle higher loads, but with fewer throws. These features, along with the robust nodular iron crankcase, enable the 560hs to handle higher gas and inertial loads.”
NEA utilized its team of engineers and designers in Germany and collaborated with the NEA USA division to develop the product specification.
The 560hs will have the typical NEA feature of a one-piece frame casting including the crosshead. The original intention of the one-piece frame construction is to ensure a perfect perpendicularity of the rod axis compared to the crankshaft axis.
“Since alignment of the frame is the most important step in the packaging process, a one-piece design eliminates wasted labor aligning bolted joints and ensures a true perpendicularity and flatness in reference to the feet and main bearing journals,” Lesak said. “Such a robust casting prevents frame twisting as well.”
Stringent FEA studies by NEA in Germany have proven this frame design to be the preferred option for both safety and cost savings. The one-piece frame eliminates bolting and gaskets between the frame and crosshead distance piece.
“Also, the main bearings feature a split design in the 90°or vertical arrangement,” Lesak said. “NEA R&D studied bearing simulations and found this increased reliability when compared to a conventional split in the 180° position. This design, along with the tri-metal material, maximizes strength of the bearing and its operational lifetime.”

In addition, the new frame has an improved design of the foot mounts for skid installation. To ease transportation, width limits were also considered. The length of the four-crank frame enables transportation without special road permits with installed cylinders and distance pieces.
Lesak said NEA’s philosophy has always been to guarantee a quick exchange of parts. Some of these parts have constant wear, such as piston rings, packing rings or cylinder bores and are known as routine spare parts. Other components are not usually viewed as routine spare parts, but can be subject to wear under unintended conditions. With that philosophy in mind, the 560hs is made with a crosshead liner that is easily replaceable. In the unlikely occurrence that a major damage event happens to the crosshead, the liner ensures the crankcase is protected.
NEA’s cylinder lineup is customizable and able to maximize the flow in the most efficient way. Power losses are minimized by combining optimized compressor valve selections, cylinder clearances and flow paths. To minimize gas leakage or fugitive emissions under all operating conditions, optimized pressure packing designs are incorporated. Finally, the complete cylinder line can be supplied in air-cooled or liquid-cooled design.
The company cooperates in component design with Stasskol, a leading manufacturer of sealing elements for oscillating and rotating systems with operations in Germany and Texas and part of the NEA Group.
Hydraulic bolting has been a standard feature on the long-stroke, large-horsepower NEA API 618 compressors for many years, and the 560hs is no different.
“Hydraulic bolting improves joint strength, ease of maintenance and, most importantly, safety,” Lesak said. “Accurate bolt loading with speed and uniformity is a cost savings highlight of this compressor. Easy-to-handle tooling and the elimination of pinch points increase the safety rating.”
The 560hs has hydraulic bolting on all dynamically loaded connections. “The most critical connection is the piston rod to crosshead, which has the highest load concentration under pure dynamic conditions,” Lesak said. In addition, this connection must be disconnected over the years when maintenance on wear parts is required. A reproducible, narrow tolerance connection is vital for the performance of the machine.
“The connecting rod bearing on the big end and all crank bearings will have their best performance and reliability when they are equally supported on their circumference, which is ensured by the bolting tension,” Lesak said. “Finally and again for safety reasons, the distance piece to frame connection, the cylinder to distance piece and anchor point connections are all hydraulically bolted up to 17,400 psi (1200 bar).”
NEA will supply the 560hs as a bare shaft compressor to select packagers or as a packaged system designed by NEA Sales and Application Centers worldwide. Standard packages compliant to ISO 13631 will be offered, but customized packages are NEA’s core competence.
“The development and introduction of the 560hs demonstrates the commitment of Neuman & Esser Group to the needs of the North American medium to high-speed compressor market,” said Scott DeBaldo, president of Neuman & Esser USA Inc. “We look forward to serving our customers and gaining new opportunities to prove that basic reliability starts with robust design.”
MAGAZINE
NEWSLETTER

CONNECT WITH THE TEAM
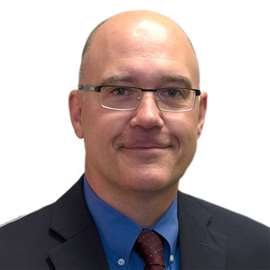
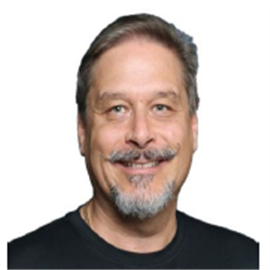
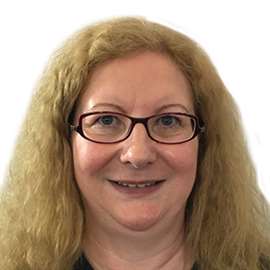
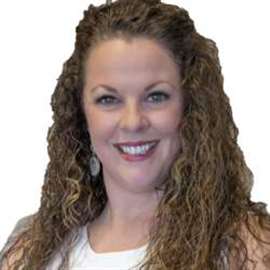