Hydrogen economy essential to decarbonization efforts
March 14, 2023

The hydrogen economy is not an imaginary prospect of some distant utopian future but increasingly, it is a reality, a panel of engineers said in a recent webinar. In response to this, the compression industry has seen a clear increase in orders for hydrogen compressors over the last several months.
“The hydrogen economy is not something for the future anymore. We are witnessing it at this moment,” said Lennert Buijs, a project manager for TNO who spoke at a recent webinar organized by the European Forum for Reciprocating Compressors.
The EFRC recently released a white paper, “Hydrogen Compression: Boosting the Hydrogen Economy,” to discuss the growth of hydrogen compression in Europe. Its recent webinar was held to unveil the main contents of that paper.
The EFRC’s paper gave an overview of the advantages and relative disadvantages of different compression systems used in the hydrogen economy. The organization highlights the existing hydrogen compression technology and the developments in Europe that support the transition towards a green hydrogen economy.
The white paper and the seminar outlined the various types of compressors available for hydrogen compression and the relative advantages and limitations of each. The hydrogen value chain can be divided into three parts: hydrogen production, transportation and storage and hydrogen end use. Compression is needed in each portion of the value chain.
Once produced, hydrogen is then compressed and fed into a transport system. It can be fed into a pipeline, which would also require compression to move the molecules to another location. It can also be transported by trailer, but compression is required here as well – and generally at even higher pressures than pipelines require.
The industry needs compression for storage in tanks or in underground gas storage. In either case, storage can buffer the intermittent nature of hydrogen production and consumption, the paper said.
Hydrogen consumption, the third link of the value chain, may also require compression that meets specific criteria depending on the application. Hydrogen can be used for power generation, as a feedstock, or as a vehicle fuel.
Europe is moving forward with multiple hydrogen projects that are designed to reduce reliance on hydrocarbons. “We see a lot of projects under development right now,” said René Peters, one of the presenters at the recent webinar.
The European Union in its Green Deal sees a significant role for hydrogen and electricity in its future energy system. In the Netherlands, for example, there are about 160 projects that would ultimately produce 12 GW of green hydrogen by 2030, he said.
The Netherlands has also committed to building a network of hydrogen pipelines that would link with a similar network in Germany and Belgium and to offshore locations. Compression would be needed throughout the pipeline network, he said.
Europe will also need compression for a growing number of hydrogen refueling stations, which need to provide high purity hydrogen at 350 to 700 bar to fuel personal vehicles or heavy duty trucks. In Germany there are 93 stations in existence and another 50 under development. Netherlands, Belgium, Denmark, Norway and Switzerland also have a growing number of refueling stations.
“We see a large rollout of hydrogen refueling stations in Europe,” Buijs said. “We are rapidly seeing a full coverage of northwest Europe for hydrogen fuel cell vehicles and heavy duty trucks.”
Some midstream operators are trying to use salt caverns and depleted gas fields for large scale storage of hydrogen. As much as 250 GW of hydrogen could be stored in salt caverns. “Storage is vital to secure a market. Caverns are needed to supply security of supply,” he said.
Various compressor types
The paper and the webinar noted that various types of compressors can be used for hydrogen and some are better fits than others depending on the application. The study compared various kinds of compressors for capacity, reliability, end pressure, purity of gas, efficiency, potential for turndown rates, pulsations, vibrations and noise.
Reciprocating compressors are among the most common because they can provide a wide range of pressures and capacities. They have a robust track record after decades in use in refineries. They are generally versatile machines that can handle changes in process conditions well and can be turned down with great efficiency. Reciprocating compressors can be lubricated or non-lubricated.
One of the disadvantages of reciprocating compressors is that they have a lot of wearing parts that need to be maintained and periodically replaced. The pressure ratio per stage is somewhat limited, which often means they need multiple stages to boost gas to a higher pressure. Reciprocating compressors also create a pulsating flow of gas that can lead to vibrations that need to be controlled.
Reciprocating compressors are the most common option for pipeline transportation of hydrogen. They are also commonly used in underground hydrogen storage applications, which typically need between 200 and 300 bar. Conditions for this application can vary and injections and withdrawals can happen several times a day.
Diaphragm and hydraulic compressors are positive displacement machines that have a good track record for hydrogen applications. They are particularly well suited for hydrogen fueling stations because they ensure a high purity of gas and can achieve greater pressure ratios per stage. They do have limitations: they generally have lower capacity than their reciprocating cousins. In addition, they require careful operation with regular service to ensure optimum reliability. Replacing a membrane in a diaphragm compressor is a relatively time consuming process when compared to replacing parts in hydraulic compressors.
Screw compressors are positive displacement machines that reduce volume of gas through a train established between two revolving rotors. One of the benefits is that they generally have a higher running speed than a reciprocating compressor, which gives it a higher capacity for the same footprint. The screw compressors have few wearing parts, which means less scheduled maintenance than reciprocating machines.
However, screw compressors have lower capacity than piston compressors and a limited track record for hydrogen because of their relatively low discharge pressure, which is usually between 30 and 40 bar. Screw compressors also generate pulsations on the outlet side, often at a higher frequency than piston compressors.
Centrifugal compressors use an impeller to accelerate and compress gases. They are considered a mature technology for hydrogen-rich applications like hydrocrackers in refineries. However, they are not well suited for pure hydrogen applications, the study found.
Centrifugal compressors can run at a high speed and have a high capacity, often higher than piston compressors of the same footprint. They have no wearing parts and their pulsations are much lower than piston compressors.
However, their pressure ratio per stage is very low and they have a limited efficiency point. They are designed to operate in a specific set of circumstances. If those circumstances change, the efficiency drops.
“Centrifugal compressors have yet a very limited track record for pure hydrogen applications,” he said.
Finally, also some more innovative concepts for hydrogen compression were discussed, using non-mechanical principles. These include, for example electrochemical compression and metal hydride compression. Though not yet at the maturity level and capacity of conventional classical (mechanical) compressors, these technologies are rapidly evolving and are of clear interest for specific hydrogen applications.
R&D trends
The EFRC has noted that many OEMs are investing heavily in research and development for hydrogen applications. There is a trend, for example, to go to increasing outlet pressure, especially for non-lubricated compressors needed for pure hydrogen.
Another trend in research is the reliability after intermittent starts and stops. Manufacturers are trying to improve the reliability of the machines that are not used at a constant rate. Hydrogen refueling stations are a prime example where a compressor would operate while a vehicle is refueled and then shut off when it is full.
Another topic of research is the possibility of hybrid compression techniques to combine relative advantages of each type of compressor. For example, some industries are studying combination of screw compressor at a low stage combined with reciprocating machine a higher stage. In other cases, they are researching the use if a reciprocating compressor at a low stage and then a diaphragm compressor at a higher stage. This combination of technologies can often be achieved on a single shaft.
Manufacturers are also researching how the different equipment used in hydrogen systems interact with each other. For example, they want to know if an electrolyzer can be damaged by the pulsations caused by a reciprocating compressor. “These are questions that are not clear yet,” said Leonard van Lier, with TNO Energy Transition.
The study made a few conclusions at the end. Hydrogen is a crucial element of the decarbonization process. Efficient and reliable compression will be needed throughout the hydrogen value chain.
In response to this surge in demand, manufacturers are looking to improve capacities and higher pressures. In addition, they are researching ways to keep equipment operating efficiently at multiple speeds and reliably with intermittent starts and stops.
MAGAZINE
NEWSLETTER

CONNECT WITH THE TEAM
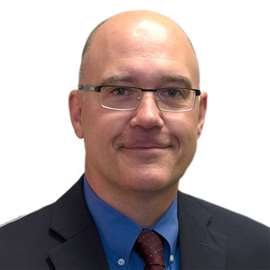
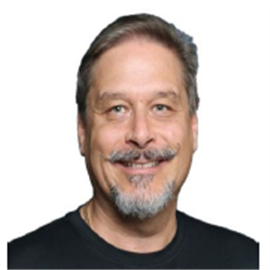
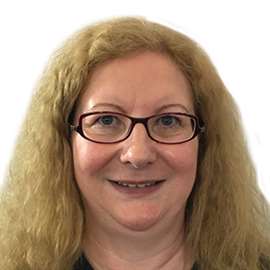
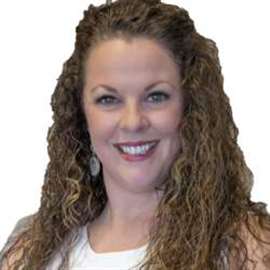