How digitization has transformed installation and commissioning
January 26, 2022
Remote management in an industrial plant: installation and commissioning
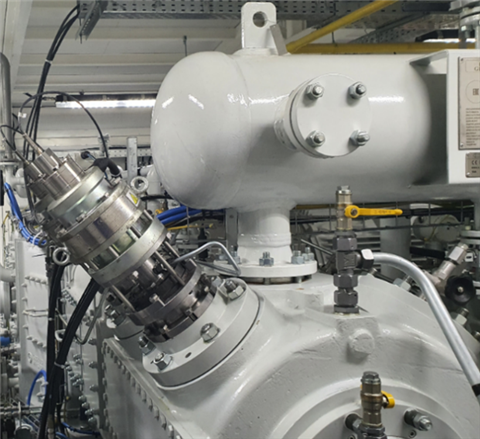
This global emergency, due to the covid-19 pandemic, has radically changed our lives and the way of approaching work. Fortunately, technology has helped us to meet our new needs, changing and in some cases improving aspects of our work.
The term Industry 4.0 refers to the rapid growth of digitization in manufacturing happening nowadays thanks to the high-speed communications enabling the transfer of big data, and to the new sensors development. The increasingly frequent use of industrial automation improves the working conditions and allows activities that would not have been possible so far. In addition, the stepless flow regulating system of reciprocating compressors is an Internet of Things (IoT) system that can be remote controlled.
This is the case of the FluxtoFlow system from Mario Cozzani, the Italian compressor valve manufacturer. The remote monitoring of the system installed in far plants is possible without the need of Cozzani team assistance on site.
This article describes how the remote connection system was applied to a real case. During this pandemic period the use of remote monitoring allowed the company to complete the installation and set-up of the FluxtoFlow system in a big plant in Russia on a LMF compressor, where it was impossible to travel due to current restrictions. This allowed an excellent punctuality in the scheduled installation and start-up phases that avoided a big waste of time and money, besides the sanitary risk.
REMOTE CONNECTION SYSTEM
The FluxtoFlow capacity control system is linked to the Cozzani Data Center through the remote connection with a VPN connection. The Cozzani Service Team can connect to the customer cabinet and the Data Centre to receive data and emails from the control boards of the installed system.
The implementation of a remote connection architecture within a stepless capacity control system has several advantages for the end user. The start-up procedure can be checked in real time by in-office technicians, in case of troubleshooting the monitoring of the real operation of each actuator/valve can easily detect and solve the faults, the maintenance activities are targeted to the real needs, maximizing efficiency and minimizing time and resources required for the maintenance operations.
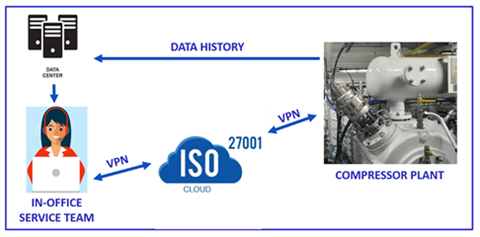
In the event of an adjustment or modification of the compressor operating conditions, the control system also allows parameter changes. This lets the system to be always tuned and highly efficient.
One of the key challenges with remote connections of the industrial control systems is the need to ensure network security, integrity and reliability. These requirements lead to the implementation of several features that must be considered to design the system. These are security protocols based on VPN connection, protected data storage, password with two-factor authentication for each operator and so on. In addition, the selection of partners with internationally recognized security standards ensures the security management, the continuous improvement on the long-term and a fully redundant network of distributed access and VPN servers.
REMOTE COMMISSIONING PHASE
The FluxtoFlow system has been chosen for an LMF reciprocating compressor installed in a hazardous area of an important refinery located in the city of Omsk, Russia. This plant produces synthetic.
The Covid pandemic did not permit Cozzani technicians to travel, so the company carried out the installation and commissioning through its remote supervision. As a result, at the end of 2020 Cozzani technical staff completed the installation and successfully put the FluxtoFlow control system in operation. The main technical specifications for the compressor are summarized in the table below:
N° stage - 2 Psuction - 10 bar(g) Pdischarge - 50 bar(g) Mass flow - 210 Kg/h Bore - 245-120 mm Stroke - 150 mm Gas Type - H2 Speed - 740 rpm |
Two electromechanical actuators with FluxtoFlow system had been installed on the suction valve cages. FluxtoFlow is a stepless capacity control system, based on the reverse flow principle. This system allows the control of the compressor flow by keeping the suction valve open for a set amount of time after the cylinder reaches the bottom dead center position. This system has been completely developed by Mario Cozzani to meet the growing need of energy saving, stability of the process and reduction of emissions.
The system remote commissioning was divided in three different steps:
Training for the technician, who would work on the plant in Russia; Cozzani technicians trained the operator through an on-site training course in our workshop.
The FluxtoFlow system installation was made by the technician on site constantly remotely supported by our reference engineers in Italy.
The start-up phase of the compressor had been performed with N2 and H2 as scheduled from the plant and our system was remotely controlled by our engineers in order to monitor the proper functioning of the flow control of our system.
Our engineers were able to give a continuous support during all the above steps concerning the operation of the FluxtoFlow and the remote assistance allowed to work directly on the system via GSM connection with the system’s power cabinet. This service also enabled the Cozzani Team to receive alarms or faults from the FluxtoFlow system in real-time, with the possibility of analysing such data and providing support as well as suggestions and/or recommendations for the client.
EXAMPLE OF REMOTE ASSISTANCE
During the installation and commissioning procedures the remote control allowed to quickly solve some issues as reported below.
Case 1: Incorrect wiring from the client
Our engineers received the following status from the FluxtoFlowTM control cabinet:
ANALOG SIGNAL |
In this case the fault reset signal 1 allowed our technician to note something wrong with the system. This signal should be constant at 0. This identified a wrong wiring at client side very quickly. In this way the technician checked the wiring set up as reported from our engineer and solved the problem in few minutes.
Case 2: incorrect wiring from the system
Our engineer, checking all the cable connections from the remote monitoring in the electric panel of our FluxtoFlow system, realized that in the terminal board there is a “spare” digital signal at some screws that was not necessary for the application. In this way he asked the plant technician to check the cables and to disconnect them from the board. They had been really connected by mistake.
Case 3: start-up tests
At the end of the systems installation the end user asked the service team to supervise the start-up of the compressor both with N2 gas and H2 gas, in order to report any problem in real time. During that supervision the capacity control had been remotely monitored and verified from our engineers ensuring the correct functioning under different degrees of capacity control with different flow.
The capability of setting up a connection with the capacity control systems allowed a reliable verification of the correct functioning of the capacity control for the compressor. The verification activity was completed without any problems by comparing the theoretical data from the datasheet and the real data acquired during the test, the system worked very well in all the cases of control.
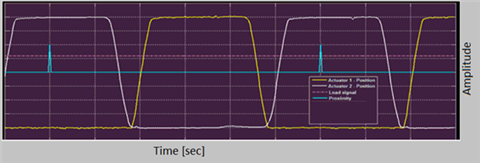
CONCLUSIONS
The described commissioning by remote of a FluxtoFlow system in a plant in Russia is a good example of the reliability of the FluxtoFlow system remote monitoring which allows critical operations to be supervised by Cozzani engineers in real time. In this case also the costs of onsite action for the commissioning and start-up phases were saved from our client. It would be possible to use remote control also for the following compressor phases, such as the operation phase and the maintenance phase, in order to have an all-around assistance. This allows a further time and cost saving required for the system management.
MAGAZINE
NEWSLETTER

CONNECT WITH THE TEAM
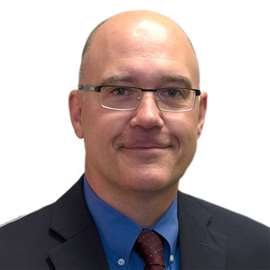
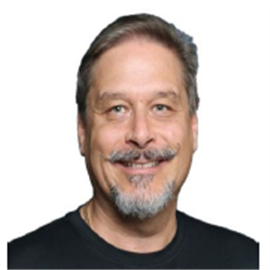
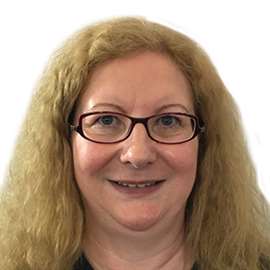
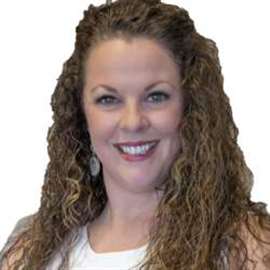