GE Brings Youth Back To Old Engines
July 14, 2017
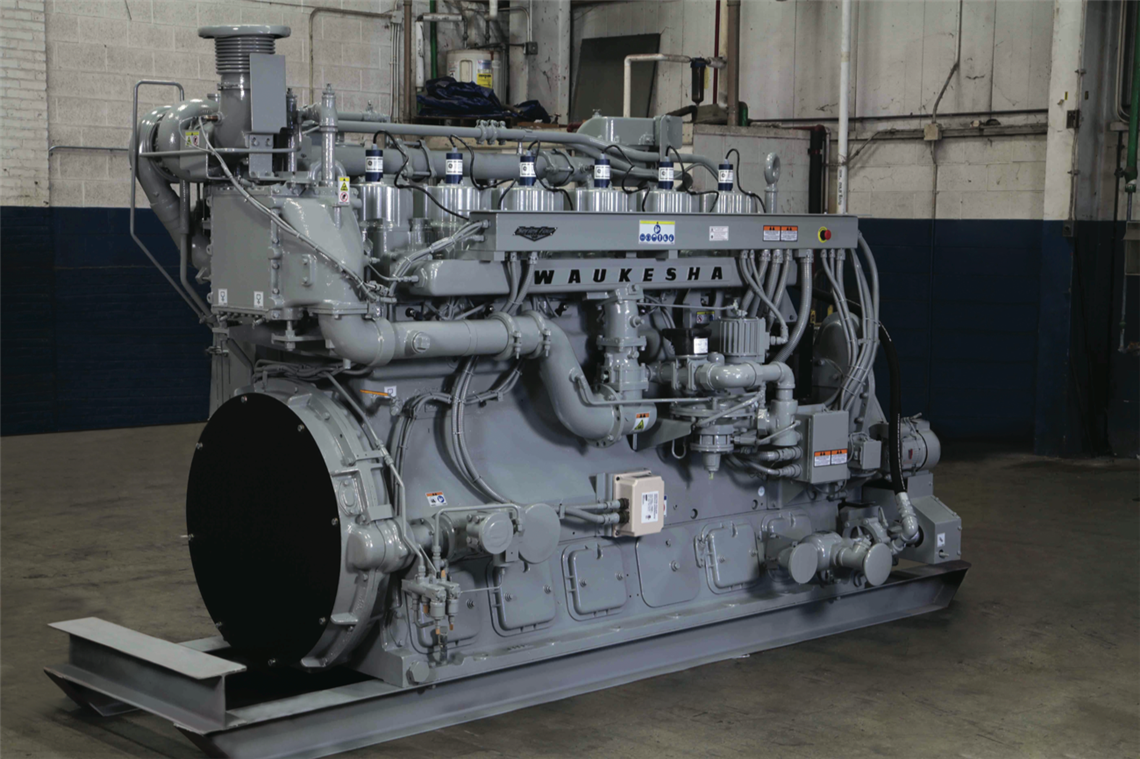
This article was originally published in the June issue of COMPRESSORtech2. We only publish a fraction of our magazine content online. For more great content like this, get every issue in your inbox/mailbox and access to our digital archives with a free subscription.
Sometimes all an old engine needs is a little love, especially when love comes in the form of conversions, modifications and upgrades.
GE’s Distributed Power has bundled a variety of options for upgrading GE’s Waukesha gas engines used in gas compression applications. Upgrades include crankcase breather kits, cylinder head and piston kits, modernized control systems, lean- to rich-burn model conversions and more.
“The Waukesha gas engine kits add opportunities to repurpose units to make them suitable for the changing gas compression segment,” said Jason Padilla, service product leader for GE’s Distributed Power. “Customers are looking for more horsepower, lower operating costs and more reliable assets.”
Archrock, a natural gas contract compression services company, fit this narrative when it reached out to GE nearly three years ago. The company, which has a 60-year legacy in the industry, rebranded as Archrock in 2015 when it spun off its global product line and non-U.S. compression operations businesses.

Archrock reached out to GE to consider options to upgrade the older model GE Waukesha VHP gas engines, which included the 7042, 5790, GL and GSI models. Archrock wanted an emissions upgrade for these engines so they could be used anywhere, no matter how strict the regulation.
The aging engines didn’t meet emissions permitting standards and didn’t offer viable performance for Archrock. Previously, GE had never provided a comprehensive upgrade that met all of Archrock’s emissions and performance requirements. After learning Archrock’s goals, GE developed a standard solution that applied to the Waukesha VHP 12-cylinder, lean-burn gas engines. The upgrade included controls and hardware, which met emissions targets while increasing power, improving reliability and reducing total cost of ownership.
Twenty-five of those gas engines were GE Waukesha 7042GL (converted to 7044GSI); two were GE Waukesha 5794LT (converted to 5794GSI); two were GE Waukesha 5790GL (converted to 5794GSI); and a GE Waukesha 5794GSI (added engine system management [ESM], emPact, Extender and air-fuel ratio [AFR2] upgrades), said Nick Klosinski, services product manager for VHP, GE Power.
After conducting the first 12-cylinder VHP upgrades, Archrock presented an opportunity for a similar upgrade on a 19-year-old, six-cylinder 2895GL VHP gas engine. At the time, a control and emissions upgrade for this model did not exist. With a series 2 to series 4 upgrade, Archrock converted the unit to a 3524GSI, but without the latest controls.



GE offered to develop its second-generation engine system manager (ESM) and emPact control product for Archrock’s six-cylinder VHP engine. This development provided a standard kit applicable to six- and 12-cylinder VHP rich-burn units.
While the upgrades are still being completed for the fleet, more than one-third of the engines have been converted, said Ryan Rudnitzki, services initiatives leader, Distributed Power, GE Power. Benefits from the upgrades include an up to 38% power uprate for the engines, a decrease in emissions (0.15g NOx, 0.3g carbon monoxide [CO] and low-volatile organic compounds [VOCs]), reduced oil con- sumption, better fuel tolerance and a lifecycle extension on major components, Rudnitzki said.
Overall, Archrock brought 20,000 bhp (14,914 kW) of added power to its fleet with the upgrades. Additionally, Archrock saved about US$150,000 per engine by opting for the upgrades instead of new engines.
Rudnitzki said the upgrades help customers bring new life to their old, idle Waukesha gas engines, as well as reduce emissions.
“It is similar to the satisfaction of finding an old house and rehabbing it or taking an old car and turning it into a classic,” he said. “From our standpoint, it is also a great way to reduce the environmental impact of the gas compression plant.”
GE Power’s upgrade catalog for Waukesha gas engines features 19 options. The one used in all of Archrock’s conversions is the emPact emission control option, which combines all of the emissions-related components of a Waukesha VHP gas engine into one control system. The system keeps the engine’s emissions in compliance by using an oxygen sensor designed specifically for natural gas operation.
The AFR2+ emPact upgrade includes a stainless-steel catalyst housing, a catalyst wiring harness, a full authority fuel valve, pre- and post-catalyst pressure and temperature sensors, a post-catalyst oxygen sensor, and an emissions control module (ECM).
Another upgrade used extensively in the Archrock engines is the ESM, which provides control capabilities to help enhance uptime and boost performance for a variety of Waukesha VHP and VGF gas engines. The ESM integrates spark timing control, speed governing, knock detection, start-stop control, diagnostic tools, fault logging, engine safeties, and air/fuel ratio control.
Some of the Archrock engines also received the advanced crankcase breather upgrade and the VHP Extender upgrade. The crankcase breather system maintains a slight negative pressure in the crankcase. This rids it of water vapors and combustion gases to prevent sludge buildup, oil contamination and oil leaks. The upgrade includes several breather components, such as a pre-separator, a separator assembly, check valve, insulation blanket and system tubing. A crankcase pressure regulator valve and mounting brackets are also included.
The Extender upgrade, according to GE Power, works well with top-end and bottom-end overhauls. The upgrade includes a crankcase breather system, an air cleaner, spin- on oil filters, a mounted oil cooler, a turbine air starter, a Microspin oil filtration unit and an optional deep sump oil pan.
“(These upgrades) are often a cost-effective way to invest your next dollar, given the current industry conditions,” Rudnitzki said. “Because the backbone (crankcase, crankshaft) of many of our products has stayed stable throughout the years, it makes a lot of sense to resurrect and redeploy current under-utilized or dormant assets rather than purchase new units.
“The best part of these upgrades is that they provide flexibility to our customers to relocate units to virtually anywhere in the world because of their low emissions,” he said.
The upgrade options aren’t expected to sit idle, however. GE Power is already looking at ways to improve its upgrade offerings in the future, Padilla said, referring to the inclusion of its ESM2, as well as combustion changes and remote monitoring.
Said Padilla, “We are well on our way to continued power increases, reduced fuel consumption and longer maintenance intervals with our next round of upgrades.”
MAGAZINE
NEWSLETTER

CONNECT WITH THE TEAM
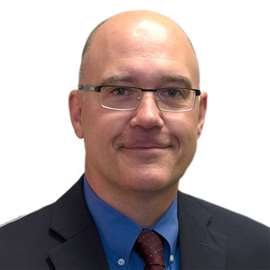
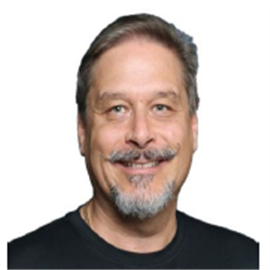
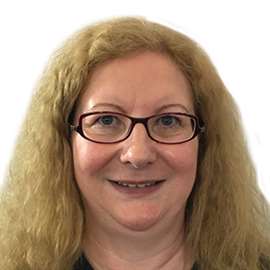
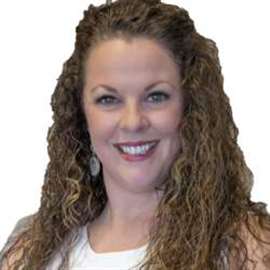