Evaluating oil sweetening for natural gas compression applications
August 08, 2023
Oil sweetening, or slipstreaming, is a relatively common practice among some operators of natural gas compressors. It involves drawing used oil from the engine and feeding it into the compressor component to lubricate the packing and cylinders of the equipment.
It’s not difficult to see why some operators have turned to oil sweetening. As long as the application is low-dilution and non-severe, it is possible to use a standard SAE 40 stationary gas engine oil to lubricate the compressor rods and packings. Using, and therefore having to stock, just one product rather than two may also seem to align with a company’s financial goals as the initial oil spend will be lower as there are fewer units and tanks to fill.
Yet some industry experts may argue that while oil sweetening can be possible for some applications, it is far from ideal. The process can affect used oil analysis reports and potentially mask issues with the engine that can cause costly repairs down the line. Using specialized compressor oils for gas compressors can also improve the performance of the equipment and actually equate to a cheaper cost per gallon than engine oils.
But it’s most important to have all the facts. In this white paper, we’ll explore oil sweetening (also commonly referred to as “slipstreaming”) from a technical perspective, consider the benefits and disadvantages of this practice, and provide recommendations for you to keep in mind.
What Is Oil Sweetening?
Oil sweetening, or slipstreaming, is a process of lubricating the compressor rods and packing of a natural gas compressor with the used engine oil. Instead of using a separate compressor oil from a different oil tank, slipstreaming involves (1) drawing suitable used oil (such as an SAE 40 grade) from the engine crankcase, (2) filtering the oil, and (3) feeding it into the compressor force feed pump and then to the (4) distributor block where it is used to lubricate the compressor rods and packing. This process of removing the used oil from the compressor then requires new supplemental oil to be added to the engine in order to maintain the engine’s oil operating level. The term oil sweetening can also be used to refer to the practice of draining a percentage of used natural gas engine oil from the engine sump and then topping off with fresh oil in order to avoid a full drain and replenishment.
Evaluating Oil Sweetening
We know that oil sweetening is popular with some operators of natural gas compressors in North America and is a relatively simple process to carry out for experienced professionals, but is it a practice that operators should be doing with their equipment?
There is no doubt that this practice can offer some benefits. But what are the risks of carrying out oil sweetening that arise when we look at the effect it can have on an operation?
In this section, we take a detailed look at the key benefits and drawbacks of carrying out oil sweetening, so that operators can make informed decisions.
The Benefits Of Oil Sweetening
ONLY ONE TANK TO FILL
A key advantage of oil sweetening is that operators only need to fill one tank of oil. Because the compressor is being lubricated using oil from the engine crankcase rather than a separate tank, oil sweetening enables you to purchase one product.
EXTENDING OIL DRAIN INTERVALS
Oil sweetening also enables operators to extend the oil drain intervals on their engine. While slipstreaming will use the same amount of oil in the compressor, the oil consumption rate on the engine is significantly increased, and more fresh oil will need to be added to the engine. This does of course reduce equipment downtime and the costs associated with regular oil changes.
LOWER INITIAL PRODUCT COST
Because the oil in the engine is continually being sweetened, a premium and therefore more expensive engine oil might not be cost justified. This clearly provides an initial upfront cost saving that, combined with only having to purchase one product, is a strong argument for operators and procurement teams alike.
The Disadvantages Of Oil Sweetening
CONTAMINATION
One crucial risk of utilizing oil sweetening is that issues can occur from the formation of gas stream contaminants such as sand, water or salt, as well as engine oil contaminants. Gas stream contaminants affect the compressor valves, packing and cylinder, as well as the lubricating oil. When combined with the detergents in engine oil (which are not present in quality compressor-specific lubricants), this can result in buildup on valves and the compressor. Foaming downstream in the process can also plug coalescer filters and contaminate the triethylene glycol (TEG) dehydration system, resulting in maintenance associated unplanned downtime and additional cleaning of the system.
EFFECT ON MAINTENANCE
Oil sweetening can also inhibit an effective maintenance program. The process dilutes the levels of wear metals and contaminants like water, coolant or silicon, masking problems that could be occurring in the engine that would otherwise be identified by a used oil analysis report. This makes it difficult for operators to know when the oil should be replaced, and therefore to predict failures. This can lead to used oil being left in applications that are slipstreaming for too long. As a result, contamination remains in the system, causing engine wear and eventual equipment failure. Oil sweetening also tends to skew evaluations of oil performance and consumption.
ENGINE WEAR
Oil sweetening can present a real risk of contaminants building up in the bottom of the sump and in circulation, or being sucked up by the oil pump in the sump and passing through the oil filters. This allows contaminants to circulate throughout the engine, filter heads, turbos and valves, increasing engine wear in boundary lubrication areas.
Filter performance can have an impact on the severity of this; however, filters can only catch contaminants of a specific size and cannot filter fine enough to remove all contaminants due to their shape or micron of the filter material.
This risk is further increased due to tighter engine tolerances and silica, which is hard and abrasive. This can wear and erode metal in boundary lubrication areas, which cannot be detected due to oil sweetening and constant dilution of wear metal through lubricant replenishment that is passed through to the compressor. This dilution also has an impact on identifying water and coolant concentration, which in turn affects lubrication.
In addition to the significant maintenance that the engine wear can cause, it could also lead to equipment failure, costly repairs and the associated production downtime.

Weighing The Options
The short-term benefits of sweetening the engine oil to lubricate your natural gas compressor cylinders are easy to calculate. A cost comparison, combined with the simplicity of handling just one oil, is persuasive for many operators. It can also be difficult to change opinions in businesses that are set in their ways and have been oil sweetening for some time.
If this is the case, it is important to get oil sweetening right in order to mitigate the clear risks that it can pose.
Oil Sweetening: Getting It Right
If you are conducting oil sweetening, make sure that these steps are followed to mitigate the risks that are associated with the process:
Use a well-suited engine oil — the engine oil should be a proper SAE 40 oil and the application must also be suited to the oil, with low levels of liquid, dilution, H2S and carbon dioxide. This can also lower pressures.
Filter correctly — the oil must be filtered to adhere to OEM specifications for the engine make and model.
Effective oil monitoring — take into account and consider the wear metals and contaminants that will be diluted in the oil.
Set realistic drain intervals — while oxidation and nitration issues are typically avoided with sweetening, it is recommended to ensure reasonable drain intervals are set and adhered to based on engine make and model, sump size, and specific operating conditions.
The long-term risks of oil sweetening can outweigh the short-term financial benefits. Oil sweetening can mask problems with the engine and can affect the downstream process or the compressor valves if the oil is not filtered properly, as well as limiting the performance of the oil itself.
Natural gas compressor packages can cost millions of dollars, so there is a substantial risk in trusting a low-cost product to extract premium performance. High-quality oils help to extend drains. This is why we recommend using a premium natural gas compressor cylinder oil to lubricate the compressor rods and packings as well as a premium stationary gas engine oil in the natural gas engine — the focus should be on how to get the most out of your equipment.
A premium engine oil will have better oxidation and nitration resistance, as well as performance at high temperatures — most engines run at over 180°F (82°C). This is combined with a better ability to clean the engine and reduce varnish buildup, which can lead to engine wear and failure.
A premium-performance product can also offer one of the key benefits of oil sweetening: the ability to extend drain intervals. In fact, a premium product can reduce the amount of oil purchased over the life of the unit and impact the total cost of operation dramatically, without the negative risks that come with oil sweetening.
A Premium Compressor Oil
The benefits of a premium compressor cylinder oil are aligned with the benefits of an engine oil. Premium compressor cylinder oils have similar qualities to the premium engine oils we’ve examined. By selecting a premium compressor oil, you can make a real difference in the overall performance and efficiency of your system.
Why?
The compressor cylinder lubrication accounts for up to two-thirds of lubricant consumption.
The compressor has unique challenges — gas quality, pressures and temperatures — and the engine oil can have an impact on them.
If foaming, valve buildup and TEG system contamination occur, it can cost days of lost production, emergency callouts and labor.
Running a product designed specifically for the compressor will increase efficiency and reduce wear, particularly by extending packing and piston life. The compressor packing and piston lubricant quality has the ability to reduce lubrication rates, extend equipment life and manage gas stream issues that affect total cost of operation.
There are hidden costs to using lower quality oil when conducting oil sweetening. But when there is no apparent problem and the way things have been done for a long time appears to be working, it may not be obvious that spending more on oil is immediately necessary. Furthermore, we understand that many companies do not have the manpower and tools to document and prove performance and the related savings.
The. With access to data, the Petro-Canada Lubricants team can review your machine performance, recommend the right premium oil and demonstrate how much it can save.
MAGAZINE
NEWSLETTER

CONNECT WITH THE TEAM
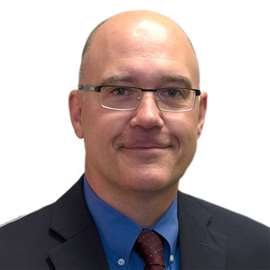
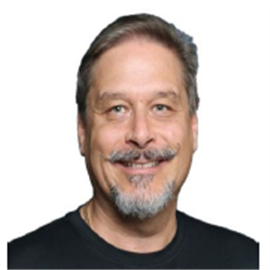
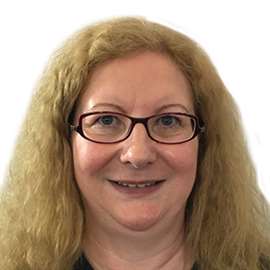
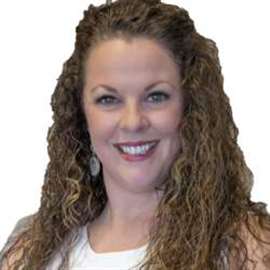