Cornerstones: The first natural gas pipelines – Part 1
July 22, 2025
The Cornerstones of Compression series has highlighted many significant products over more than 160 years of continuous progress. This is the first of six Cornerstones of Compression corollary articles that provide a look back at the evolution of natural gas pipelines and compressor stations.
Largely hidden from view, a cornerstone of the natural gas compression industry was the development of safe, reliable pipelines. In the early days of U.S. oil patch development, gas was a waste product unless it could be used near the well that produced it. Enormous gas wells were discovered, but gas was viewed as a “worthless commodity” that was flared or simply allowed to escape to the atmosphere. The idea of piping it over long distances to make it a marketable commodity had not been conceived.
The first oil pipeline was a 5-mile (8-km), 2-in. (51-mm) diameter wrought iron pipe constructed in 1865 near Pithole, Pennsylvania. Though initially ridiculed, pipelines competed with the railroads and teamsters transporting oil in those days. John D. Rockefeller said the whole industry would have been held back without the development of pipelines.
Since natural gas could not be contained in a barrel and hauled, development of underground pipelines was necessary for reaching distant markets.
Made of wood
The first gas pipelines were made of wood, beginning in Fredonia, New York in 1821. In 1823, gas bubbling out from along the south shore of Lake Erie was captured and piped through pine logs to a lighthouse. Wooden pipes were used for manufactured gas in several New York cities as early as 1854, with some still in service as late as 1929.

The genesis of thousands of miles of long-distance underground pipelines throughout the U.S. began with a bold experiment that failed miserably. In 1870, work began on a 25-mi. (40-km) pipeline from West Bloomfield to Rochester, New York.
Large iron pipe was rare at the time and steel pipe didn’t exist yet, so hollowed out pine tree trunks were used. Bands of iron were shrunk around 2 to 8-ft. (0.6 to 2.4-m) long hollowed out logs, which were coated inside and out with tar.
Joints were sealed by dipping the end of a log in hot tar and driving it into another log. Wooden logs had little flexibility, so turns were very gradual. Iron gate valves were inserted in the line at frequent points, an example of which is shown in Fig. 1, excavated after years of service.
As the New York project progressed, gas flowed along the pipe, and as each valve was placed, it was closed to hold back about 8 psig (0.6 bar) for leak tests. Valves were not closed tight, fearing that the well pressure might blow the line apart. Leaks were repaired by wrapping pipe with tar-soaked strips of burlap or surplus Civil War blankets, secured in place by two half rings of iron bolted together.
The project was a major engineering feat at the time. At first, there were few leaks, and a good flow of gas at a suitable pressure was carried to within 5 mi. (8 km) of Rochester. Then, high pressure built up and the pipeline blew apart.
The line was eventually completed to reach Rochester in 1872. But it was plagued by leaks and by water and mud seeping into the line and freezing. When demand was low, pressure would build up and burst the pipes. The line was soon abandoned.
First use of iron pipe
The first use of iron pipe for a “long distance” gas line occurred in 1872. Cast iron pipe had been around since the 1840s, and cast and wrought (ductile) iron pipes of various diameters were commonly used at oil well sites. A 2 in. (51 mm) wrought iron pipeline from Newton to Titusville, Pennsylvania enabled 90 psig (6.2 bar) wellhead pressure to push gas about 5 mi. (8 km).
In 1876, a 17 mi. (27 km), 6 in. (152 mm) cast iron gas line was laid from Butler County to Etna, Pennsylvania to supply an iron works at a pressure of 119 psig (8.2 bar). Other iron and steel works in Pittsburgh were supplied in the 1880s by new pipelines flowing from area wells, including one that George Westinghouse had drilled on his estate.

Harper’s Magazine in 1886 reported that natural gas in Pittsburgh was already displacing over ten thousand tons of coal daily.
In 1885, Rockefeller interests laid an 8 in. (203 mm) wrought iron line from Oil City to Titusville, part of which remained in service for 70 years. In 1889, the Equitable Gas Company fabricated a 21 mi. (34 km), 36 in. (914 mm) pipeline from 0.25 in. (6.4 mm) steel plate, riveted together and caulked to prevent leakage.
In 1886, an 87 mi. (140 km), 8 in. (203 mm) wrought iron line with threaded couplings was built from Kane, Pennsylvania to Buffalo, New York. It was still in use in 1973, when it was “renewed” by inserting a 4 in. (102 mm) plastic line inside it. A parallel 8 in. (203 mm) line in 1898 used Dresser couplings instead of threaded joints for the first time. These “self-packing” couplings with rubber seals, developed by Solomon R. Dresser, allowed this pipeline to operate at 250 psig (17.2 bar).
Labor intensive
Construction of early pipelines was very labor intensive. Pipeline trenches were dug with picks and shovels. Workers swinging eight-pound hammers onto a drill shaft cleared rocks and made tunnels under hills of solid rock. Once the random lengths of iron pipe were hauled in with teams of mules pulling wagons or sleds, they were screwed together and tightened by tong gangs as shown in Fig. 2.
It took almost 70 years after discovery of the first gas well in Fredonia, to figure out how to transport gas more than 100 mi. (161 km).
In 1891, two parallel 120 mi. (193 km), 8 in. (203 mm) threaded wrought iron pipelines were constructed from near Greenwood, Indiana with wellhead pressure of 525 psi (36.2 bar) to Chicago, Illinois.
Soon after 1900, natural gas spread to industrial centers like Cincinnati, Cleveland, and Toledo, Ohio.

MAGAZINE
NEWSLETTER

CONNECT WITH THE TEAM
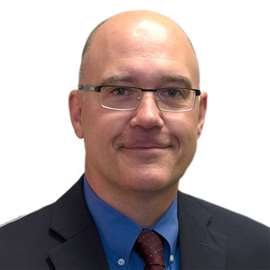
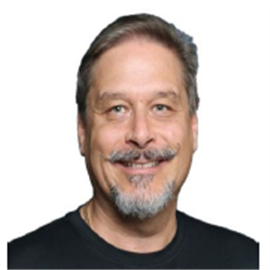
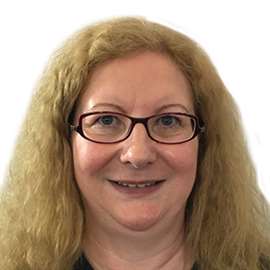
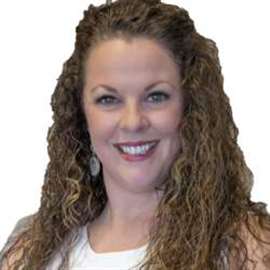