Cornerstones Corollary: Great Ideas That Didn’t Make It!
November 06, 2023
The Cornerstones of Compression series has highlighted many significant products and companies over more than 160 years of continuous progress. However, there were also some great engine and compressor ideas that were unsuccessful
The Cornerstones of Compression series has highlighted many significant products and companies over more than 160 years of continuous progress. However, there were also some great engine and compressor ideas that were unsuccessful. Starting with this issue, this brief Cornerstones of Compression corollary series features several notable product development failures.
The Dresser Radial Gas Engine-Compressor
Although decades ahead of its time, the unsuccessful high-speed gas engine-compressor development led to the unexpected formation of Dresser-Clark.
In 1930, virtually all the natural gas pipelines in the U.S. were laid with couplings supplied by the S. R. Dresser Manufacturing Co. Highly profitable, the company was looking for expansion opportunities. Dresser observed that other than pipe, compressors were the greatest expenditure for pipelines.
Pipelines were making quantum jumps in length and needed more powerful compressors to push the gas farther. Dresser felt that the engine advancements of automobile, airplane and marine industries, especially in valve improvement, could be borrowed for more economical, smaller, lighter and higher-speed compressors.
Dresser had no experience in designing compressors, but its management and engineers lacked neither the ambition nor the capital for such an undertaking. Howell Cooper, a prominent gas engineer with Hope Natural Gas Company had planted and promoted the idea of a radial engine and compressor. Following the pattern of airplane engines, cylinders would mount radially around a shaft instead of horizontally. A unit of this type should require less space, be lighter, less expensive and yet more powerful. Early in 1931, Dresser quietly began work on what was at first called the Howell High-speed Compressor. The “Cooper” name wasn’t used because Cooper-Bessemer was already the largest producer of gas engine-compressors.
Funding for the project was set, with the goal of having the first unit “completed and perfected” by January 1932. But when that time soon arrived, the much-anticipated radial engine and compressor was nowhere near completion. Unforeseen complications seemed to arise every day to thwart the ambitious project as expenses mounted.
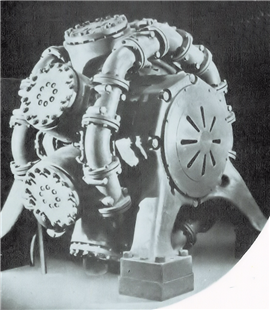
Despite the effects of the Great Depression causing the company’s first loss in 1933, Dresser was unwavering, noting that natural gas engineers were more enthusiastic than ever about the radial unit. Orderly progression of technology required a series of intermediate steps before a distant goal could be reached, but this unit was aiming to skip these steps. It was to operate at 1250 rpm, not the conventional 250 rpm, but with this fivefold increase, the machine was smaller and lighter than existing units. Parts customarily used on standard compressors were not adaptable for the radial. Essentially, each component had to be developed from scratch. For example, when a new spark plug was needed, Dresser had to develop one itself. Elaborate experiments were conducted to find steel durable enough for the high-speed valves, and inevitably the tests took longer than anticipated.
The first experimental model was finally ready for testing in early 1934, but it failed to function satisfactorily and changes were necessary in the valve construction. However, the forecast was that later that year Dresser would be ready to accept a few trial orders before the next season of maximum gas demand.
But the redesigned units were not ready for field testing until November 1935. The first engine was connected to an electric generator in the Dresser plant, developing more than 600 hp (447 kW) and performing satisfactorily. A second unit was in the field, pumping gas continuously into a pipeline.
The radial machine had an “ungainly appearance,” so an industrial designer was hired to transform its external image from a “confusion of pipes and joints” into a sleek unit encased in steel. But problems continued with lubrication and vibration. Potential customers, observing the field unit’s problems, began to lose interest, and Dresser decided that it was time for an outside source to evaluate if the radial engine and compressor was truly feasible. The consultants’ conclusions were favorable, but they noted that Dresser did not have enough engineers with experience in compressors and its production facilities were inadequate for the ambitious task. Upon receipt of the consultants’ report, the board of directors approved additional funding to construct two or three new units, and the company began seeking a more experienced team of engineers and a better production facility. They did not have to look far, as some 20 miles (32 km) away was the Clark Bros. Company. Although Dresser’s compressor would be in competition with its own units, Clark Bros. needed the work, so was happy to work on the project, although skeptical about its practicality.

Before 1936 ended, success seemed at hand. The Columbia Gas & Electric Co. agreed to buy one of the radial units for its Sugar Grove field. A handsome color brochure entitled “Dresser Presents an Engineering Achievement!” boasted of “the beginning of a new development of the economics of gas transportation.” The compact unit was mounted in two self-contained sections on a common bedplate and connected through an all-metal flexible coupling. The eight-cylinder 8 in. bore x 8 in. stroke (203 x 293 mm) water-cooled, two-cycle radial engine generated 500 hp (373 kW) at 1000 rpm. The compressor was a four- or eight-cylinder 8 in. (203 mm) stroke radial. Dresser seemed on the verge of the long-awaited technical and marketing breakthrough.
Dresser’s other businesses were prospering, and although it remained optimistic about the radial’s future, another interesting and unexpected opportunity had arisen as a result of the radial development project. Clark Bros. Company had an excellent reputation with fine engines and compressors that were sold worldwide, but the Great Depression had seriously impaired its financial integrity. Dresser’s acquisition of the Clark Bros. Co. in July 1937 turned out to be a tremendous move for both companies.
Sometime in 1939 the radial engine and compressor project was finally abandoned. Developed at a cost of well over half a million dollars, it was quietly discontinued after the sale of just eight units. The goal of power with light weight had been achieved, but the units were simply too light for continuous operation at high speeds. However, the disappointment was made easier by the unexpected success achieved by the Clark Bros. Company’s new and much heavier model RA angle engine-compressor. By 1940, having adequate capital for growth, Clark Bros.’ sales exceeded that of all the rest of Dresser’s businesses. And in many ways, the radial project created a pattern for Dresser-Clark to invest in significant research for years to come.
MAGAZINE
NEWSLETTER

CONNECT WITH THE TEAM
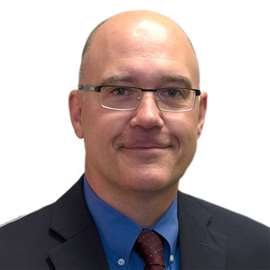
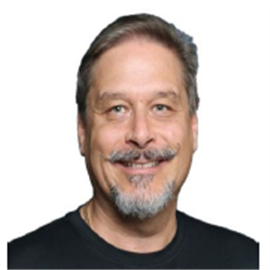
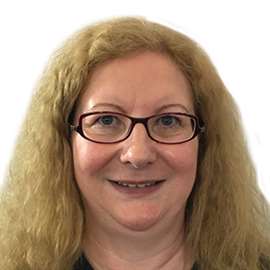
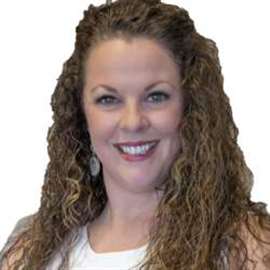