Coating Solutions for Centrifugal Compressor Fouling
October 30, 2020

Several options available to mitigate build up in high-use machinery in a variety of applications, environments
Author’s Corner: Derrick Bauer is a supervising engineer, Materials Engineering Department, with Elliott Group.
Corrosion and fouling of centrifugal compressors during operation are major concerns in the petrochemical industry. While the cause of an electrochemical (corrosive) attack depends on several variables, corrosion and its effects are readily visible and well understood. In most circumstances, the selection of a base material that is suitable for the process gas application will minimize a corrosion attack.
Fouling, or the buildup of solids on the compressor’s internal surfaces, is a more process-dependent issue. In hydrocarbon services, foulant is caused by a polymerization reaction intrinsic to the compression process. Foulant buildup limits flow through the compressor and can alter the compressor’s aerodynamics, reduce efficiency over time, increase vibration and result in an unplanned shutdown.
Many variables affect the occurrence of fouling and the exact process is not always fully understood. These factors make predicting the amount of fouling expected within a centrifugal compressor impossible to determine with any amount of certainty. The focus, therefore, needs to be on how to best minimize the amount of foulant depositing on the aerodynamic surfaces of the compressor or, if possible, prevent fouling from forming in the first place.
Read the rest of the story here.
This article was originally published in the May 2020 issue of COMPRESSORTECH2. We only publish a fraction of our magazine content online, so for more great content, get every issue in your inbox/mailbox and access to our digital archives with a free subscription. Click here for a new subscription or here to renew your current subscription.
MAGAZINE
NEWSLETTER

CONNECT WITH THE TEAM
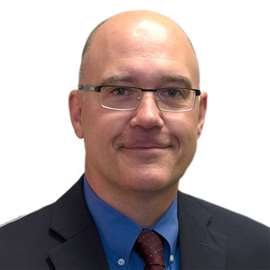
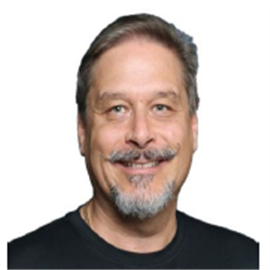
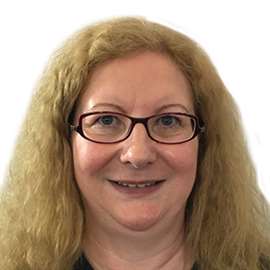
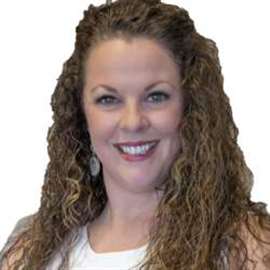