Big leaps for smallest molecule
July 08, 2024
Raimondo Giavi, vice president of hydrogen at Baker Hughes, shares with COMPRESSORtech2 advancements on hydrogen technology. By Roberta Prandi
Operations with hydrogen is not recent news for Baker Hughes: the company built its first hydrogen reciprocating compressor in the 1910s. With such a massive log of experience in the field, the company pioneered the energy transition looking at the opportunities related to hydrogen early on and has made quantum steps since.
Raimondo Giavi, vice president of hydrogen at Baker Hughes, explained that the company’s strategy for hydrogen covers different aspects: “First we have of course continuous development on our conventional products for hydrogen compression and handling. Besides compressors, where our competences date back to over 100 years, we have prime movers such as the first commercially viable gas turbine running on 100% hydrogen.
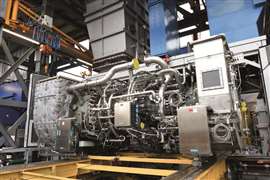
“We should not forget other components that are very important for a safe and efficient use of hydrogen though: pumps and valves in the first place, but also everything related to sensing technology, monitoring and diagnostic, which are key in this particular field.”
The second aspect is standardization and modularization of the product portfolio: “This approach is fundamental in this market, since the biggest barrier in developing hydrogen production, infrastructure and handling is cost. It goes without saying that standardizing components for a modular approach helps significantly in lowering costs.”
Another aspect for Baker Hughes is the development of solutions for low-carbon hydrogen production: “We are investing in technologies such as methane pyrolysis technology; anion exchange membrane (AEM); solid oxide electrolysser cell technology (SOEC); and field testing methane plasma technology,” said Giavi. “We call these Generation 2 and 3 solutions that follow incumbent technologies to help reducing cost, increasing efficiency and scaling up application to what is required for the energy transition.”
Baker Hughes signed an agreement with ADNOC in 2023 to study and pilot the deployment of innovative solutions from Baker Hughes’ hydrogen portfolio.
The collaboration includes next-generation electrolyzer technology to explore the possibility of installing and operating an electrolyzer at the ADNOC Research and Innovation Center (ADIRC) in Abu Dhabi; field testing methane plasma technology to capture carbon in the form of high quality graphene and hydrogen in ADNOC Gas’ facilities; and testing the use of methane pyrolysis technology to produce low-greenhouse gases intensity hydrogen.
The collaboration builds on ADNOC’s $15 billion commitment towards decarbonization projects by 2030.
And finally, another key aspect being explored by Baker Hughes is maintenance and service. Giavi said that currently the post-sale service for products dealing with hydrogen is an area still a bit overlooked, since these technologies are new and not many players are already thinking ahead at the post-sale scenario. Not so for Baker Hughes, which is developing a specific hydrogen maintenance approach based on the practices and experiences gathered after many years of servicing more conventional components.
According to Giavi: “Basic service practices are essentially the same, but there is an incredible opportunity with the application of digital solutions, where a hydrogen economy presents an almost completely clean slate to experiment and adopt the resulting best solutions.”
Within Baker Hughes’ hydrogen strategy, the official unveiling of the new Hydrogen Testing Facility a few months ago represented a major milestone.
The Hydrogen Testing Facility was used for the validation of NovaLT16 industrial turbines to run blends all the way up to 100% hydrogen.
The new facility includes a test bench to allow full load testing, with complete fuel flexibility up to 100% hydrogen and features a 300-bar pressure and 2,450 kg hydrogen storage capacity. This infrastructure, aligned to the highest standards of safety and security allows Baker Hughes to test turbines in all project conditions, providing customers with enhanced operational confidence.
Giavi explained, the NovaLT16 gas turbine for 100% hydrogen operation features a new three-channel combustion system that allows to modify the fuel blend on-the-fly and under any load.
“What is really impressing is that this turbine can be started directly with pure hydrogen, thanks to a special design for flame control,” he added. “Hydrogen flame is very volatile and cold start is therefore a bit more problematic to manage than that of gas.”
Another characteristic of the NovaLT16 for 100% hydrogen operation is the fuel mixing skid that is mounted separate from the turbine. Giavi explained the mixing skid would not be necessary at all in case the gas turbine could run on pure hydrogen without any natural gas back-up. An instance which is for now still a bit distant from realization, with the exception of very few projects based on hydrogen production where supply would not be an issue.
“One example is the new net-zero hydrogen energy complex of Air Products in Edmonton, in the Province of Alberta, Canada. Baker Hughes already supplied Air Products with advanced hydrogen compression and gas turbine technology, including NovaLT16 turbines.”
As far as hydrogen compression is concerned, Giavi already mentioned the very early days of Baker Hughes reciprocating compressors for hydrogen at the beginning of the 20th century, “In more recent times though, Baker Hughes was the first to start developing centrifugal compressors specifically designed for hydrogen,” he said.
The current status with hydrogen centrifugal compressors is the 2ND Generation HPRC (high pressure ratio compressors) compressors. Development is ongoing for 3rd generation of these compressors, which are expected to be a game-changer for the hydrogen compression industry.
According to Giavi, one of the design goals for the 3rd Generation compressors is to reduce footprint: “We have started from the standard design of our centrifugal compressors and taken them to their very physical limits. In fact, by keeping the same package size and doubling the speed of the compressor wheel, we can significantly increase the quantity of handled hydrogen and reach higher compression levels.
“Higher speed though brings major stresses to the materials. Thus, the choice of materials such as unconventional special alloys and the adoptions of some other expedients.”
Giavi concluded by explaining that the Hydrogen Testing Facility at the Baker Hughes headquarters in Florence is just the first step to the realization of a Hydrogen Village.
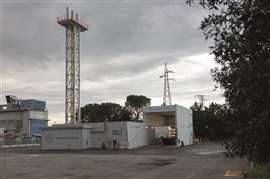
Giavi commented that one of the major challenges to future hydrogen developments is the lack of standards and regulations for hydrogen handling in urban environments. For now, the only available regulations are those in place for refineries, fertilizers plants, and such.
“Currently, projects related to hydrogen are being launched in many countries and all seem to be proceeding on their own path. We miss a common approach to hydrogen trading and a standardized system for hydrogen ‘certification, or at least having set parameters that will allow to match certifications among different countries.”
MAGAZINE
NEWSLETTER

CONNECT WITH THE TEAM
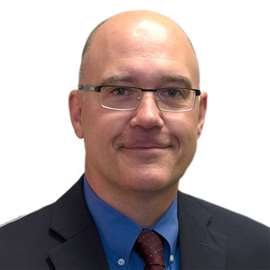
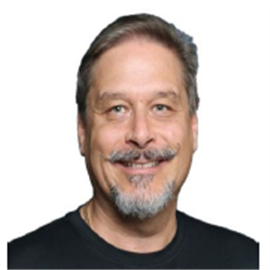
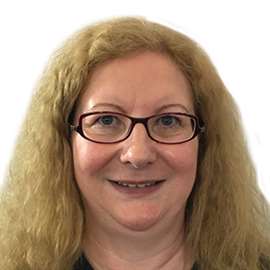
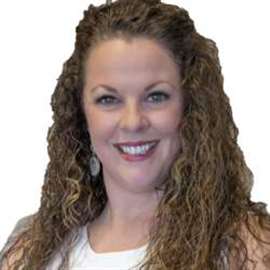