An alternative to traditional concrete foundations
November 29, 2021
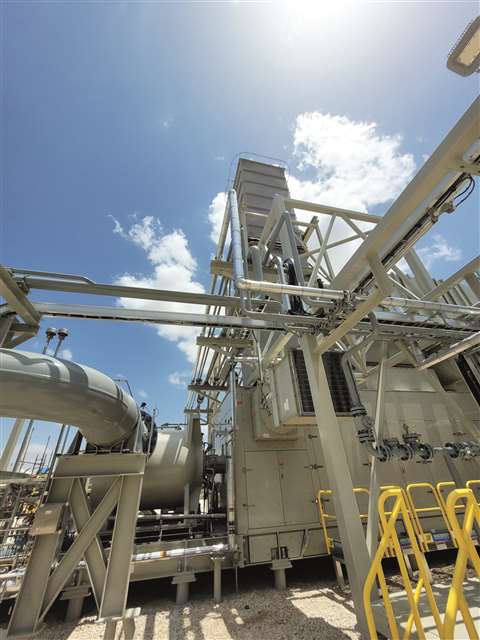
The technology to direct mount compressors on screwpiles makes it possible to build entire compressor plants with virtually no concrete. With the ongoing industry focus on reducing cost, maintaining a schedule and lowering carbon footprint, Alpine Site Services offers a unique and innovative solutions for industrial construction projects.
Screwpile foundation systems have been utilized in the construction industry for decades to support statically loaded equipment in all soil conditions. Screwpiles are making an increasing presence in supporting dynamically loaded and reciprocating equipment.
Screwpiles are well known in the construction industry for expediting construction schedules in some of the roughest climates and soils conditions, said Josh Bolling, an engineer and project manager at Alpine.
With the ability to support axial loads up to 200 kips, and large lateral loads using larger and/or battered piles, screwpiles are being effectively designed to manage and mitigate both vibration and resonance in dynamically loaded systems while saving time and cost.
A general rule of thumb is that traditional slab foundations need about five times the mass of the skid itself to stabilize the vibrations from the operating compressor. A slab of that size can take up to four weeks to completely cure.
Screwpile foundations for reciprocating compressors can be in place in as little as two to three days, without any delays for forming, pouring, and curing. A screwpile foundation for a turbine can be in place in as little as half a day, he said.
By partnering with Southwest Research Institute (SwRI), a San Antonio, Texas-based engineering and design institute, Alpine provides screwpile foundations for reciprocating compressor packages, using its patented direct-mount system.
Alpine has mounted reciprocating compressors ranging from 1800 to 4800 hp and turbine compressor packages without the need for and structural concrete or grout.
Alpine Site Services has used screw piles to mount large reciprocating equipment without the need for concrete or grout. The company has more than 20 years of experience with screwpiles, and more than 10 years mounting large reciprocating compressors on them.
Alpine has proven that screwpiles are a feasible solution to the challenges facing the compression industry.
For reciprocating compressors with more than 1800hp, SwRI conducts on-site pile/soil dynamic testing under the direction of Alpine. The tests are designed to establish the natural frequency and spring constant for the piles used for the design of the compressor foundation, Bolling said.
SwRI incorporates this data into a finite element model to design the screwpile foundation for the compressor. This assures the compressor will perform as designed once in operation and avoids long-term maintenance and efficiency costs.
SwRI conducts additional post operational testing to ensure the foundation performs as designed. The first round of test is conducted after the compressor and skid are mounted and a second round of test is conducted after all of the piping is connected.
MAGAZINE
NEWSLETTER

CONNECT WITH THE TEAM
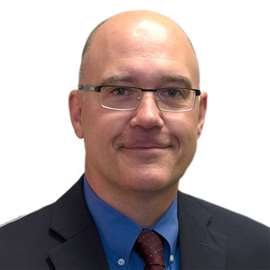
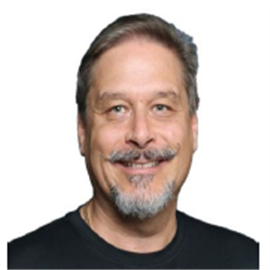
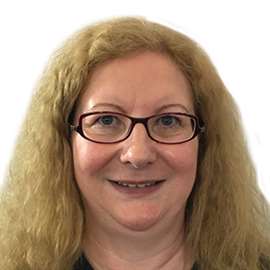
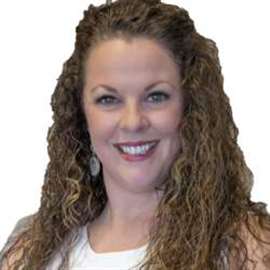