Alternative energy leads to renewed interest in processing assets
February 17, 2022

The ongoing efforts to slash carbon emissions in search of alternative energy sources has led to a lot of soul-searching in the energy industry as companies struggle to develop new products for sources of alternative energy. One company that has embraced the challenge is Arvada, Colorado-based Sundyne, a maker of industrial pumps and compressors used in multiple industries, including the energy industry.
Tom Helmreich, Sundyne’s global engineering & technology director, said the company has received a large influx of inquiries over the last year from potential customers in search of technologies that enable the development of alternative energy, including hydrogen and carbon capture.
As the lightest element, hydrogen poses unique challenges to the industry, but Sundyne has made hydrogen compressors for a long time in the refining industry, where it is used to clean up fuels and remove sulphur.
“We have extensive hydrogen experience,” he said. “Hydrogen has typically been in refining. We learned how to seal it and how to manage the equipment.” Refiners typically use compressors to circulate hydrogen through a catalyst, where the differential pressure is very low. “You are just getting it to move along and you can do that with a centrifugal compressor,” he said.
These newer, retail applications, such as hydrogen refueling stations, don’t use centrifugal compressors, but instead require diaphragm compressors, like Sundyne’s PPI compressors.
“In the retail space, you’re trying to take hydrogen out of an electrolyzer that might be at 15 psi and get it to 8000 or 10000 psi. And that is where a diaphragm compressor excels. It can get those very high compression ratios,” he said.
In general, refiners who process hydrogen use centrifugal compressors while the retail applications call for diaphragm compressors. But there are exceptions, he said. Occasionally, diaphragm compressors are used in refineries. “Where you will see a PPI compressor in a more conventional plant is when they are using hydrogen in small quantities and injecting it in a reactor,” he said. “You will sometimes see a diaphragm compressor in a refining or a midstream process, but it is not really core to that process.”
But the effort to decarbonize the energy industry has led to a surge in other technologies, such as carbon capture and storage, which still require centrifugal compressors.
The company’s traditional centrifugal compressors are useful for handling carbon dioxide. “Centrifugal compressors work real well because carbon dioxide is a lot heavier than hydrogen. That’s a sweet spot for the kind of compressors that we have,” he said.
Sundyne is traditionally known for its centrifugal compressors, but is now aggressively targeting hydrogen applications with its PPI line of diaphragm compressors.
“What’s unique about Sundyne is the breadth of our portfolio,” said Sundyne Chief Commercial Officer Aaron Bridges. “We don’t have just one solution for one opportunity. When we come in and work with a customer, we look at the overall ecosystem of what they are trying to achieve. It’s a whole carbon play all the way through the value chain.”
Sundyne is planning investments in blue and green hydrogen. It has compressors and pumps that work with electrolyzers and in hydrogen refueling stations. The company has seen orders for technologies that allow end users to safely boost pressures and lower emissions double over the last 12 months.
“Our machines allow us to split and push product into areas that make the most sense for the plant to be most efficient so the end user can achieve its ESG goals,” Bridges said. “We can mix and match our equipment to help the customer do what they want.” Its products are used in LNG plants, cryogenic gas plants and gas gathering systems.
The ongoing drive to reduce emissions has led to a growth in interest in carbon capture technologies, which typically require centrifugal compressors. Sundyne’s Pinnacle compressors or its BMC integrally geared centrifugal gas compressors have been used in amine scrubbing units, which have been used to remove CO2 for decades.
The drive to find alternative energy sources has brought new entrants into the industry, many of whom are not experts in separation or transport of gas or water. “They come to us and say ‘here’s what we’ve got. How do you dry it up? How do we pressure it up?’” Helmreich said.
“If you think of a hydrogen refueling station in a retail setting: they don’t have people who know how to change pump seals. They don’t have people who know how to change diaphragms in compressors. They want that service covered by the companies that sell those systems. It’s going to be the same with carbon capture. You have a bunch of dispersed sources with small systems collecting carbon. That’s going to change the complexion for aftermarket support. It will require different service networks with local parts, better inventory and quick turns,” he said.
MAGAZINE
NEWSLETTER

CONNECT WITH THE TEAM
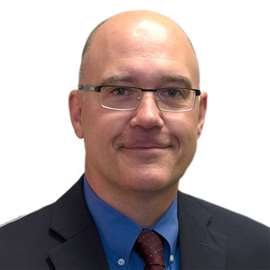
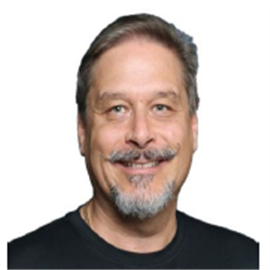
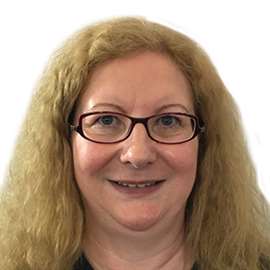
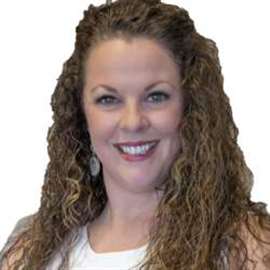