A Quick Scan For Quality
July 12, 2019
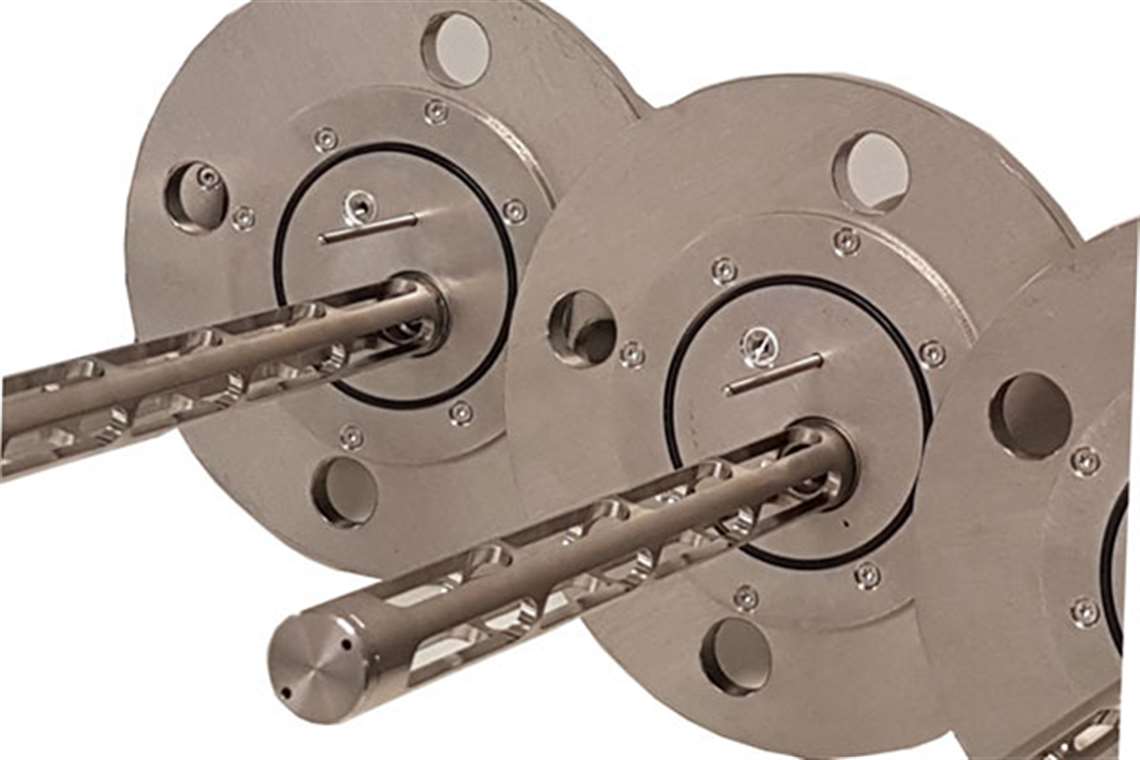
The new NIRIS (near infrared intelligent sensor) natural gas sensor from CMR Group is designed to reduce consumption levels of natural gas engines through real-time measurement of fuel quality.
The term “natural gas” covers a wide range of qualities of gas derived from the main component, methane (CH4), according to Patrice Flot, chief technical officer at CMR Group, who presented a paper on the NIRIS at CIMAC in Vancouver, British Columbia, Canada. Indeed, the quality of gas can change at a given location and these changes could be rapid when switching from one source to another.
Most gas engines are sensitive to the methane index. Gas with a high methane index (80 to 90) will provide smooth combustion starting from the spark ignition device, while gas with a low methane index (55 to 65) enhances the risk of knocking by auto-ignition at several places inside the combustion chamber, Flot said.
The new NIRIS NG sensor is designed to measure methane number through measurement of CH4, C2H6, C3H8 and C4H10 content and has a response time of less than one second. The sensor works on optical principle and can be simply plugged into the gas supply pipe of engine — it doesn’t require a sampling piping system. Light is emitted by the sensor and travels through the gas inside the supply pipe on the engine before being analyzed by a detector. The output signal from the detector is a simple spectrum that is then processed by a calculation matrix to provide gas composition and related parameters.
It also incorporates a CAN bus communications facility, which enables the system to be upgradeable without dismantling the sensor for improved performance and retro applications, although retrofit applications are possible only if supported by the engine builder.
Linked to electrical actuators, the sensor is designed to enable instantaneous adjustment of the engine for critical situations, including the switching on and off of valves on a gas network to change gas supply from one source of gas to another one of different quality, switching gas supply from network piping to local storage tank and reverse, switching engine supply from an empty liquid natural gas (LNG) tank to a full LNG tank and on heavy seas, where variable load on the propulsion might require variable forced boiloff be added to natural boil-off, resulting in highly variable methane number at engine entrance.
Further, by combining a thermal conductivity sensor also designed for fast response time to the NIRIS NG sensor, it is possible to measure H2 injection rate into the natural gas within one second. This provides a new solution to control combustion of gas engines with a variable H2 injection rate, according to Flot.
Natural gas consumption levels can be further reduced by engine tuning closer to knocking limits due to effective fuel management strategies using sensor data. Other benefits include lower fuel analysis costs, correct engine performance and the overall alleviation of time consuming and costly damage to components due to inferior or low-grade gas fuels, according to the company.
France-based CMR Group designs, manufactures andcommissions automation, control system and turnkey project solutions for globalindustrial and renewable energy sectors, alongside specialized instrumentationfor high power diesel or gas engines.
-By Jack Burke
MAGAZINE
NEWSLETTER

CONNECT WITH THE TEAM
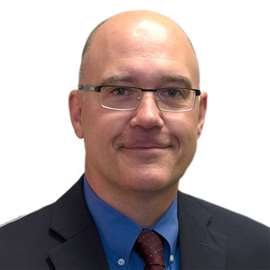
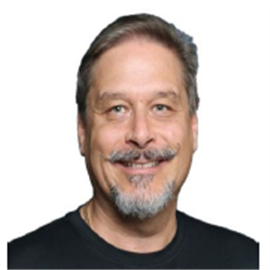
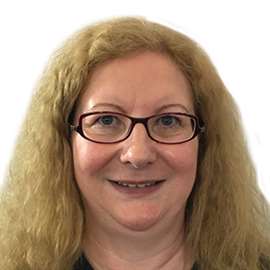
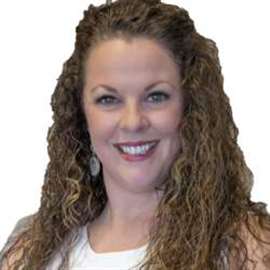