A growing hydrogen market?
August 28, 2024
Screw compressors could fill a gap, MAN ES believes.
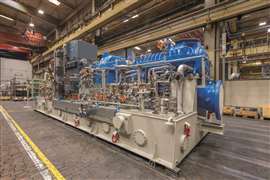
MAN Energy Solutions (MAN ES) has manufactured screw compressors for more than 70 years. The company’s screw compressors were first used in a hydrogen application in 1974 at a refinery in Middle East.
Now the company has found a new – and potentially vast – hydrogen market for its technology.
Recently the company has received two orders for its screw compressor technology for hydrogen electrolyzer projects, said Dirk Woeckener, head of sales, screw compressors, MAN ES.
One project is a 200 MW electrolyzer in France and is part of a development of renewable and low-carbon hydrogen sector, to contribute to decarbonizing industry in the region of north France.
Woeckener said MAN screw compressors will be coupled with reciprocating compressors – a match that will offer the strengths of both technologies.
“The screw compressor’s volume flow offers many possibilities, but it is limited in regard to the discharge pressure,” Woeckener said. “Depending on the requirements, a combination of a screw compressor with a reciprocating compressor is often used. The screw compressor is placed directly downstream of an electrolyzer operating on low pressure when there is a relatively large volume flow. This setup helps avoid the challenge of needing a reciprocating compressor with a piston diameter of 1 m or more. So since the screw compressor is reducing the volume flow directly downstream of electrolyzer and afterwards, the reciprocating compressor is making the high discharge pressure.”
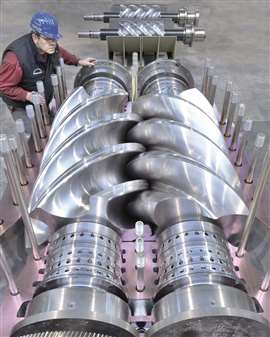
Woeckener said the company is seeing a lot of interest from the industry for its technology.
“This is a new business opportunity for us,” Woeckener said. “We’ve seen many studies and received many inquiries beside the two orders. There is a lot in the pipeline.”
Advantages to the technology
MAN’s oil-free screw compressors are used in various applications, including the chemical and petrochemical industries as well as in steel manufacturing. They are designed to handle difficult conditions, such as contaminated gases, according to Woeckener.
“They are an ideal solution for handling very dirty and critical gases,” Woeckener said. “We can inject a high amount of water – more than it would evaporate – so that we have liquid water in the compressor, which protects it against particles.”
That same technology is being used in the hydrogen applications, not because of dirty gas, but to increase the efficiency due to the low molecular weight,” Woeckener explained.
Woeckener mentioned that the company’s two series of screw compressors – the CP and SKUEL – achieve volume flows between 200 and 100,000 cubic meters per hour. The CP series is designed for higher pressures, up to 52 bar, and medium flows up to 20,000 cubic meters per hour. The SKUEL series offers a discharge pressure up to 16 bar and is suitable for high volume flows up to 100,000 cubic meters per hour.
“The screw compressor is an ideal solution for a hydrogen producing electrolyzer because it combines the advantages of reciprocating compressors and centrifugal compressors,” Woeckener said. “Like the reciprocating compressor, it is a positive displacement machine, so we have advantages in regard to low molecular weights because we can achieve high pressure ratios per compressor stage. However, unlike reciprocating compressors, which have valves that are subject to wear and tear and also have oscillating masses, screw compressors have only rotating parts, like centrifugal compressors. This results in very high reliability for uninterrupted service, comparable to a centrifugal compressor. These machines can operate for three to five years without interruption.”
Seal technology
While MAN ES has deep experience working with hydrogen, the company decided to upgrade its seal technology for use in electrolyzer application.
“We have all types of seals available for different applications,” said Jan Schnitzler, head of engineering, screw compressors at MAN ES. “These include dry seals, mechanical contact seals, carbon rings and labyrinths. For hydrogen applications, we introduced a new sealing design in collaboration with our seal suppliers.
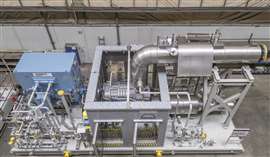
This new sealing concept has several advantages. During operation the seal guaranties zero emission of hydrogen to the environment. Furthermore, this eliminates the need for nitrogen or any other gas or liquid as a buffer, Schnitzler said. So, it is only water coming into the hydrogen and the hydrogen remains completely clean. The seal can generally use the water required for the electrolyzers, which is beneficial since the water is already present.
“We have to take special care in terms of conductivity, which has special requirements, but in general, we can use almost the same water,” Schnitzler said.
Schnitzler also highlighted that leakage from new sealing technology “is minimal, keeping operating costs low.”
The future of hydrogen
Woeckener said that, as the hydrogen economy grows, there will be more opportunities for screw compressors.
“When it came to hydrogen, most people were talking about reciprocating compressors only,” Woeckener said. “I think reciprocating compressors will continue to play an important role in hydrogen compression because they are relatively cheap, efficient, and well-established in the market.”
The challenge starts when large volumes are needed, which requires larger pistons and more difficult maintenance. When the diameter approaches one meter, maintenance becomes challenging and expensive.
“Screw compressors are a very reasonable alternative for volume flows starting from about 8000 cubic meters per hour,” Woeckener said. “We’re currently seeing applications of 50 to 300 MW but also requests for even larger projects, which are suitable for screw compressors.”
Woeckener also mentioned that the company expects future applications for centrifugal compressors when the amount of hydrogen becomes even greater, such as in pipeline compressors. Current electrolyzer projects being developed are geared towards local distribution network rather than feeding pipelines.
As soon as the hydrogen production scales up significantly, Woeckener believes all types of compressor technology will be needed.
“The requirements for hydrogen are so big, and it is such a difficult molecule, that I think all types of compressors will be necessary to fulfill these demands,” Woeckener said.
MAGAZINE
NEWSLETTER

CONNECT WITH THE TEAM
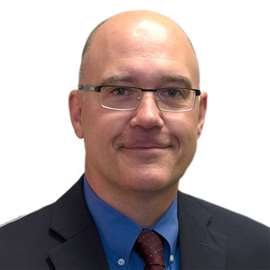
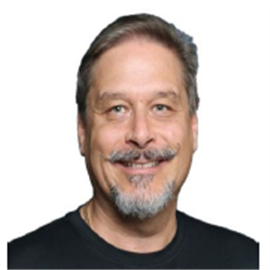
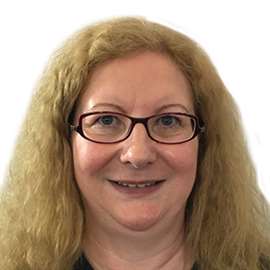
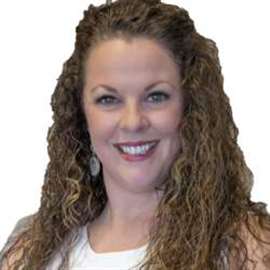