Compressors are hydrogen ‘colour blind’
August 11, 2022

Hydrogen is poised to play a crucial role in the energy transition and has emerged as a powerful decarbonization agent for many carbon-intensive sectors, including process industry, transportation, mobility, and power generation.
Compressors are an essential part of the hydrogen value chain and are needed to efficiently transport and store hydrogen from its point of production to end-use. This includes the gathering of emissions-free “Green” hydrogen produced by electrolyzers; “Grey” hydrogen from steam methane or autothermal reformers (SMRs/ATRs); or “Blue” hydrogen, which is essentially “grey” hydrogen with CO2 removed from the generating source. Other applications include transporting hydrogen via short or long-distance pipelines, compressing it to the pressure levels required by vehicle fueling stations, fuel cells, supplying gas turbines, or other downstream and petrochemical processes.
Hydrogen compressors do not “see” the hydrogen production method “colour”, as every process produces the same low molecular (i.e., mole) weight hydrogen gas. However, there are several factors that must be considered when selecting a machine for a given application. In this article, we will discuss a few key variables, including:
- Gas Composition
- Water Content
- Wet vs. Dry Process Gas Flow
- Suction Pressure
- Process Gas Temperature
- Compression Ratio
- Cylinder Lube-oil Carryover
For end-users, failure to specify these values to OEMs submitting bids can result in a number of undesirable outcomes, including higher costs (in both CAPEX and OPEX) and confusion as to which compressor solution is best suited for the application.
Hydrogen Compression Basics
Hydrogen has a mole weight of 2.02 g/mol and a density approximately 1/8th that of natural gas. This has important implications for compression as each compressor technology is impacted differently basis the low gas mole weight.
Reciprocating compressors work on the principle of positive displacement; therefore, efficiency is not affected by the molecular weight of the process gas compressed. This is in contrast to centrifugal-type turbo-compressors, which utilize high-speed impeller rotation to increase the kinetic energy of the gas which is then converted to pressure through the stationary diffuser. The gas kinetic energy is a direct function of its velocity and mass (molecular weight). Since the mole weight of hydrogen is low, the velocity of the gas will need to be higher to achieve an equivalent pressure compared to a heavier mole weight gas.
Increasing the kinetic energy can be done two ways: the first is increasing impeller tip speed by increasing rotational speed and/or expanding the diameter of the impeller. The limiting factor here is often the mechanical strength limits of the impeller materials. The second is by incorporating additional compressor stages.
Currently, state-of-the-art reciprocating compressors can achieve a given overall compression ratio in fewer stages than turbo-compressors. For example, achieving a pressure ratio of 4:1 on hydrogen gas would typically require only two stages in a reciprocating compressor. With a turbo-compressor, the same application may take as many as six stages and would likely come at a higher CAPEX as well.
While turbo-compressors have limitations in hydrogen service, progress is being made on advancing the technology for improving compression ratio capabilities. Research and development efforts are currently focusing on several areas, including the design of the core compressor, bearings, materials, seals, train architecture, and packaging.
Ultimately, the choice of compressor will be dictated by the unique requirements of the process. Turbo-compressors are generally a better option for situations with moderate to high flows and lower compression ratios (i.e., hydrotreating units in refineries). Reciprocating compressors, on the other hand, are better suited for lower volumes and higher pressures, or where a high range and flexibility in part-load operation is expected. A prime example would be downstream of an electrolyzer unit in a green hydrogen production plant.
Design Considerations for Reciprocating Compressors
Siemens Energy is a leading provider of both reciprocating and turbo-compressors to the hydrogen market. With over 2,500 reciprocating units (more than 2.5 million horsepower) installed worldwide in hydrogen rich services, the company has extensive experience designing these machines for a wide range of applications. To ensure optimal compressor solutions are obtained, the impacts of critical process parameters need to be clearly understood. Some of the most important are outlined below.
- Gas Composition - Gas composition dictates gas compressibility and gas molecular weight. It is possible for different gas mix combinations to have the same combined molecular weight but different compressibility values. This is critical, as compressibility will impact power consumption of the compressor, which in turn will affect motor selection and lifecycle costs of the plant. Generally, a lower molecular weight will require larger cylinders vs. the equivalent mass flow of a higher molecular weight gas. Specifying the exact make-up of the gas to the compressor OEM (i.e., 100% H2 vs. 99% H2, 1% O2) will ensure that the correct design is selected, and that costs and energy consumption are optimized.
- Water Content & Wet vs. Dry Flow – Water content also impacts gas molecular weight and compressibility. 100% dry hydrogen gas will have a lower molecular weight than 100% hydrogen gas saturated with water. A gas containing water can have its flow represented as a “dry flow” where the water content is not considered or as a “wet flow” which does take water into account. A wet gas application will typically require a smaller compressor solution if it is sized on the basis of wet flow rather than the same value as a dry flow. Additional scope and material considerations may also be required if water is present in the gas.
- Suction Pressure - Reciprocating compressors are highly sensitive to suction pressure, especially near atmospheric (1 BarA). This is because positive displacement machines need to physically create the volume to be compressed. A unit compressing gas at 1BarA will require first stage cylinders roughly twice the volume of the equivalent service compressing the gas from 2 BarA. This sensitivity is noticeable even when comparing 1.05 BarA to 1.1 BarA. Therefore, it is important to be precise when defining the pressure as “atmospheric”.
- Gas Temperature - A higher temperature gas will require larger bore cylinders to create the same volume as a lower temperature gas at the same pressure. Compressing a gas with a higher suction temperature will have a higher discharge temperature. This can result in discharge temperature limits being reached sooner, thus additional stages of compression may be required.
- Compression Ratio – As mentioned previously, achieving higher compression ratios requires additional stages of compression; and additional stages require additional cylinders. Compressor staging requirements will also be influenced by discharge temperature limits. For hydrogen, depending on process gas temperatures, the compression ratio per stage would typically be around ~2.
- Lube-oil Carryover - Lubrication provides protective film for wear parts and is critical to compressor reliability and availability. To improve reliability and availability, non-lubricated services require a slower piston speed. This is met by reducing electric motor RPM, or shortening the compressor stroke. Reduced piston speed will necessitate larger bore cylinders to meet equivalent flow capacities. Non-lube applications have lower discharge pressure limits and bore diameter limitations.
To illustrate how even slight changes in the above parameters will impact compressor selection, let us examine a hydrogen compression application with the following requirements specified by the end-user:
- Application: Green Hydrogen (Electrolysis Plant)
- Suction Pressure: Atmospheric
- Discharge Pressure: 30bar
- Hydrogen Production Volume: 420 kg/hr
- Now although it seems the provided data by the end-user is complete, the data is in fact open enough to allow two different compressor OEMs submitting bids for the project to make their own assumptions about several parameters. These assumptions are included in Figure 2.

Based on these assumptions, the design and cost difference between the compressors specified by the OEMs are substantial.
For OEM 1, the solution might look like:
- 3 cylinders
- 3 stages of intercooled compression
- ~500 kW motor
- ~$2MM CAPEX
Whereas, OEM 2 would have a different solution:
- 6 cylinders
- 5 stages of intercooled compression
- ~900 kW motor
- ~$3MM CAPEX
The OPEX of both solutions is difficult to quantify without a more detailed description of the site parameters and client operating philosophy. However, we can see that the discrepancy in total cost of ownership (TCO) would be further compounded when comparing the two solution’s power consumption and different maintenance requirements.
The Road Ahead
Through 2050, global production of hydrogen is forecast to reach as high as 750 million tonnes per annum (mtpa) – a 10-fold increase from the 74 mtpa produced in 2018 [1]. However, to realize its full potential in the global Energy Transition, the production of hydrogen must be decarbonized dramatically. This means accelerating the build out of both “blue” and “green” hydrogen capacity. Today, 95% of all hydrogen is still “grey”, with associated emissions of around 9-10 tons of CO2 per ton of hydrogen produced [2].

Figure 3. Compressors are needed at virtually every step of the hydrogen value chain
Compressors are an enabling technology and are needed at virtually every step of the hydrogen value chain. Regardless of the hydrogen application or the type of compressor being used (reciprocating or turbo), end-users can benefit by engaging early with OEMs to clearly define the requirements of the process, as well as any potential constraints. Doing so ensures right sizing of the compressor and that design attributes are selected which will provide the lowest TCO over the life of the unit.
With a broad compression portfolio and 100+ years of experience in hydrogen compression, Siemens Energy can remain compressor “neutral”, thus ensuring that the optimal equipment solution is selected, no matter the colour of the hydrogen.
References:
1. Strategy and Part of the PWC Network, The dawn of green hydrogen.
2. H2 Compression: An Integral Part of the H Value Chain’, Siemens Energy, (2021).
MAGAZINE
NEWSLETTER

CONNECT WITH THE TEAM
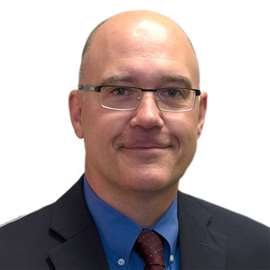
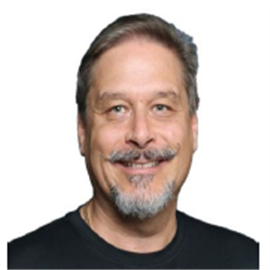
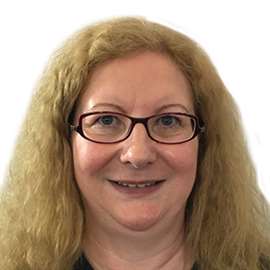
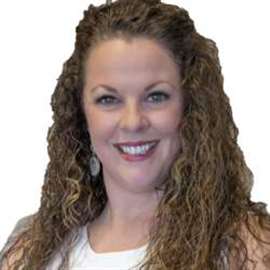